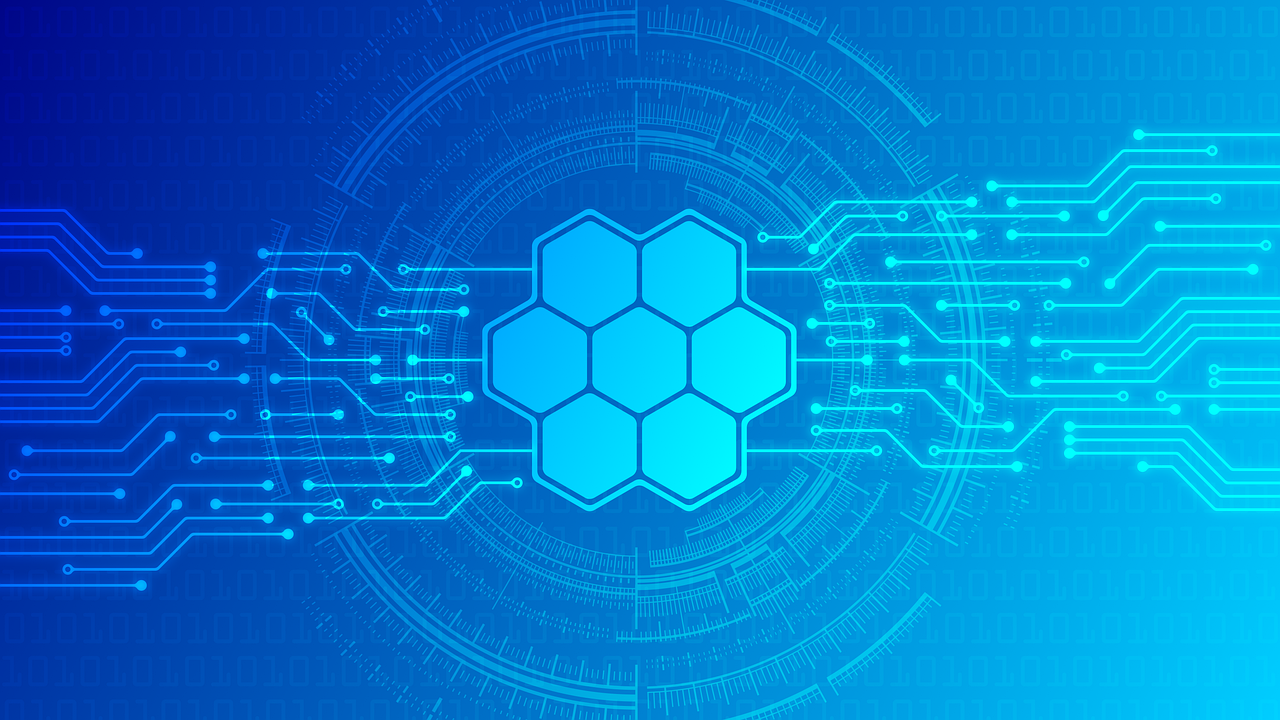
TECH TALK
High Reliability Insights From ES Components
The Official Blog of
Key Challenges in Medical Integrated Circuits Today
Medical integrated circuits (ICs) are at the heart of modern healthcare, powering everything from implantable devices to diagnostic equipment. However, as technology advances, engineers face a growing set of challenges that demand innovative solutions. Here’s a deeper dive into the most pressing issues shaping the industry today
Medical integrated circuits (ICs) are at the heart of modern healthcare, powering everything from implantable devices to diagnostic equipment. However, as technology advances, engineers face a growing set of challenges that demand innovative solutions. Here’s a deeper dive into the most pressing issues shaping the industry today.
1. Regulatory Compliance and Quality Assurance: The High-Stakes Barrier
Unlike consumer electronics, medical ICs must meet stringent regulatory standards such as FDA, ISO 13485, and IEC 60601. Compliance isn’t just a checkbox—it requires rigorous design validation, traceability, and testing protocols. Any failure can delay product launches or even lead to costly recalls.
2. Cybersecurity: The Hidden Threat in Connected Devices
With the rise of wireless and IoT-enabled medical devices, cybersecurity is a growing concern. Pacemakers, insulin pumps, and hospital equipment are now potential targets for cyberattacks. Engineers must implement robust encryption, authentication, and real-time monitoring to ensure both patient safety and data integrity.
3. Supply Chain Disruptions: Securing a Stable Component Pipeline
Global semiconductor shortages, geopolitical tensions, and reliance on a handful of suppliers make sourcing high-reliability components a challenge. Engineers must design with supply chain resilience in mind—finding second-source components, using adaptable architectures, and considering longevity in part availability.
4. Power Efficiency & Thermal Management: The Ultimate Balancing Act
Medical ICs, especially for implantable and wearable devices, must deliver high performance with ultra-low power consumption. Managing heat dissipation in a tiny package is another challenge—excess heat can damage tissue or degrade sensor accuracy. Innovations in power management ICs (PMICs) and energy harvesting solutions are key to overcoming these limitations.
5. Patient Safety: Designing for Zero Failure
Reliability isn’t optional in medical electronics—lives depend on it. Engineers must ensure fail-safe designs, redundancy mechanisms, and extensive testing under real-world conditions. Radiation exposure, biocompatibility, and electromagnetic interference (EMI) all add layers of complexity to the development process.
6. The Ever-Changing Regulatory Landscape
As medical technology evolves, so do the regulations. Engineers must stay ahead of shifting global standards, from cybersecurity mandates to new approval pathways for AI-driven medical devices. Agility in adapting to regulatory changes is critical for bringing products to market.
7. Industrial Design Meets Engineering: Sterilization & Durability Challenges
Medical ICs often need to function in extreme conditions—exposed to repeated sterilization cycles, fluids, and harsh disinfectants. Designing circuits that withstand these environments without degradation is a tough materials-science challenge, requiring innovation in encapsulation, coatings, and hermetic sealing.
8. Intellectual Property & Counterfeit Risks
Counterfeit ICs are a growing problem in high-reliability sectors, including medical devices. Engineers and manufacturers must implement robust sourcing strategies, authentication methods, and supply chain tracking to prevent compromised components from entering critical applications.
9. Mixed-Signal IC Design: Where Analog Meets Digital Complexity
Many medical ICs operate in mixed-signal environments, requiring precision analog circuitry alongside high-speed digital processing. Challenges such as noise mitigation, power efficiency, clock distribution, and signal integrity require sophisticated design techniques and specialized tools.
10. Physical Defects: The Hidden Enemies of Reliability
Medical ICs must withstand long-term operation without failure. Common failure mechanisms include:
Gate-Oxide-Shorts and TDDB (Time-Dependent Dielectric Breakdown), which degrade transistor performance.
ESD (Electrostatic Discharge), which can destroy delicate circuitry.
Electric Field Stress, leading to unexpected degradation over time.
Reliability testing, robust packaging, and defect mitigation strategies are essential to extend device lifespan.
Conclusion: Engineering the Future of Medical ICs
As medical technology continues to evolve, engineers are at the forefront of solving these complex challenges. From designing ultra-low-power chips to securing devices against cyber threats, the next generation of medical ICs will require innovation, adaptability, and precision. The future of healthcare depends on the ability to push these boundaries—while ensuring safety, reliability, and compliance every step of the way.
Why Aerospace Customers Rely on High-Reliability Microelectronic Components
In the aerospace industry, reliability isn’t just a priority—it’s a necessity. Aerospace systems operate in some of the harshest environments imaginable, where even the smallest electronic failure can lead to catastrophic consequences. That’s why high-reliability (hi-rel) microelectronic components are the backbone of mission-critical aerospace applications.
In the aerospace industry, reliability isn’t just a priority—it’s a necessity. Aerospace systems operate in some of the harshest environments imaginable, where even the smallest electronic failure can lead to catastrophic consequences. That’s why high-reliability (hi-rel) microelectronic components are the backbone of mission-critical aerospace applications.
Why Reliability Matters
1. Extreme Environments
From the searing heat of reentry to the freezing void of space, aerospace electronics must endure extreme temperatures, intense vibrations, radiation exposure, and relentless mechanical stress. Ordinary components simply won’t survive.
2. Mission-Critical Operations
Failure is not an option in aerospace. Whether controlling an aircraft’s flight systems, powering a satellite’s communications, or navigating a deep-space probe, these components must function flawlessly—every time. A single failure could mean loss of life, mission failure, or millions of dollars in damages.
3. Longevity & Durability
Unlike consumer electronics, aerospace components must last for decades without failure. Satellites, aircraft, and spacecraft are expected to perform reliably over extended lifetimes, often in environments where maintenance is impossible.
4. Performance at the Highest Level
Aerospace applications demand precision, speed, and efficiency. Hi-rel microelectronics provide the power and processing capabilities required for cutting-edge avionics, satellite communications, and advanced guidance systems.
5. Safety & Security
Passenger safety, crew security, and mission success all depend on the integrity of these components. Every electronic system must be fail-safe, resilient, and protected against external threats, including electromagnetic interference and environmental hazards.
6. Meeting Stringent Industry Standards
Aerospace electronics must comply with rigorous military and industry standards, such as MIL-STD-883 and MIL-PRF-38534, ensuring they meet the highest levels of quality, reliability, and durability.
Key High-Reliability Components
1. Semiconductors
Critical components like transistors, diodes, and integrated circuits are engineered to function under extreme conditions while maintaining optimal performance.
2. Passive Components
High-reliability resistors, capacitors, and inductors ensure stable electrical performance in aerospace systems.
3. Connectors & Cables
Built to withstand extreme temperatures, vibrations, and radiation, aerospace-grade connectors and cables provide secure and uninterrupted connections.
4. Advanced Packaging
Hermetic ceramic packaging enhances durability by protecting components from radiation, heat, outgassing, and mechanical shock.
Where Hi-Rel Microelectronics Are Used
Avionics: Flight control, navigation, and communication systems
Satellites: Power distribution, sensors, and communication modules
Spacecraft: Propulsion systems, life support, and scientific instruments
Aircraft: Engine controls, landing gear, and onboard electronics
ES Components: Your Partner in High-Reliability Solutions
At ES Components, we specialize in supplying high-reliability microelectronic components tailored for aerospace, defense, and other demanding industries. Our extensive range includes semiconductors, integrated circuits, and passive components that meet stringent industry standards. With a commitment to innovation and quality, we provide tailored solutions that ensure long-term reliability and performance in even the most extreme environments.
When failure is not an option, ES Components delivers.
Why Customers Choose Microchip Technology’s SIlicon Carbide (SiC) Products
When performance, efficiency, and reliability matter most, Microchip Technology's Silicon Carbide (SiC) solutions stand out. Designed for high-power applications, our SiC products deliver unmatched efficiency, faster switching speeds, and resilience in extreme conditions—all leading to smaller, lighter, and more reliable systems.
When performance, efficiency, and reliability matter most, Microchip Technology's Silicon Carbide (SiC) solutions stand out. Designed for high-power applications, our SiC products deliver unmatched efficiency, faster switching speeds, and resilience in extreme conditions—all leading to smaller, lighter, and more reliable systems.
Key Benefits of SiC Technology:
Unmatched Efficiency – SiC devices slash energy losses compared to traditional silicon, making them perfect for power-hungry applications while cutting operational costs.
Superior Thermal Management – Built to thrive in extreme heat, SiC ensures stable performance in demanding environments where thermal stability is critical.
Lightning-Fast Switching Speeds – Process high power levels at unprecedented speeds, optimizing high-frequency applications for superior performance.
Extreme Voltage & Current Handling – Designed to endure higher voltages, currents, and temperatures, SiC technology excels in high-demand applications.
Rugged & Reliable – With robust avalanche performance, SiC components withstand sudden power surges, preventing failures and enhancing system durability.
Smaller, Lighter Designs – Higher power density enables compact, lightweight systems, a game-changer for electric vehicles, solar inverters, and aerospace applications.
Extended EV Range – SiC boosts electric vehicle efficiency, extending range by over 7%, giving automakers a competitive edge.
Where SiC Technology is Powering the Future
🔹 Electric Vehicles – Driving greater efficiency and longer range
🔹 Solar Inverters – Maximizing energy conversion for sustainable power
🔹 Industrial Motor Drives – Enhancing performance and reliability
🔹 Residential Heat Pumps – Enabling more efficient, cost-effective home heating
Microchip: Your Partner in SiC Innovation
As a leader in SiC technology, Microchip provides a robust product portfolio and intuitive development tools to help customers design best-in-class power solutions. Whether you're building the future of EVs, renewable energy, or industrial automation, Microchip’s SiC solutions give you the competitive edge.
Ready to Upgrade? ES Components Has Microchip SiC In Stock!
At ES Components, we understand that quality, availability, and support are just as important as performance. That’s why we proudly stock Microchip SiC Bare Die, ready to ship when you need them.
🔹 Reliable Supply Chain – Avoid long lead times with our ready-to-ship inventory
🔹 Made in the USA – Ensuring top-tier quality and compliance with industry standards
🔹 Trusted Partner – Supporting aerospace, military, medical, and industrial markets
📦 Contact ES Components now to secure your Microchip SiC components!
Streamlining Supply Chains: How ES Components Optimizes Vendor Managed Inventory (VMI) for Mission-Critical Industries
In industries where precision, reliability, and efficiency are critical—such as aerospace, military, medical, and industrial manufacturing—effective supply chain management can mean the difference between operational success and costly delays. Vendor Managed Inventory (VMI) is a powerful solution that ensures businesses have the right components when they need them, reducing lead times, minimizing stockouts, and optimizing inventory levels.
In industries where precision, reliability, and efficiency are critical—such as aerospace, military, medical, and industrial manufacturing—effective supply chain management can mean the difference between operational success and costly delays. Vendor Managed Inventory (VMI) is a powerful solution that ensures businesses have the right components when they need them, reducing lead times, minimizing stockouts, and optimizing inventory levels.
ES Components specializes in VMI solutions tailored to the unique demands of these mission-critical industries, offering expertise and strategic inventory management that helps businesses stay ahead.
What is Vendor Managed Inventory (VMI)?
Vendor Managed Inventory (VMI) is a supply chain strategy where a supplier takes responsibility for maintaining an agreed inventory level at the customer's facility or a designated warehouse. Instead of traditional inventory management, where the customer places orders when stock is low, VMI shifts the responsibility to the supplier, ensuring a steady flow of critical components. This system enhances efficiency, reduces the burden on procurement teams, and ensures that production lines remain uninterrupted.
The Challenges of Supply Chain Management in Mission-Critical Industries
Industries such as aerospace, military, and medical manufacturing face unique challenges in supply chain management:
Strict Quality and Compliance Requirements: Components must meet rigorous standards to ensure reliability and performance.
Long Lead Times: Many high-reliability electronic components have extended manufacturing cycles, requiring strategic inventory planning.
Obsolescence Risks: Rapid technological advancements can render components obsolete, necessitating proactive inventory strategies.
Unpredictable Demand Fluctuations: Changes in project timelines, government contracts, or unforeseen market demands can disrupt supply chain planning.
How ES Components Enhances VMI Solutions
ES Components provides a structured, proactive approach to Vendor Managed Inventory, ensuring that businesses operating in mission-critical industries can streamline their supply chains with confidence. Here’s how we do it:
1. Data-Driven Inventory Optimization
We utilize advanced data analytics to monitor usage patterns, forecast demand, and optimize stock levels. By analyzing historical trends and real-time data, we ensure that the right components are always available, reducing the risk of stockouts or excess inventory.
2. Customized Inventory Solutions
Every industry has unique needs. ES Components works closely with clients to develop customized VMI programs that align with production schedules, compliance requirements, and risk management strategies. Whether it's buffer stock for high-priority components or just-in-time inventory for lean manufacturing, we tailor solutions for maximum efficiency.
3. Strong Supplier Relationships and Sourcing Expertise
With decades of experience in the high-reliability electronics sector, ES Components has built strong relationships with key suppliers. Our expertise in sourcing ensures a steady supply of components, even when facing global shortages or supply chain disruptions.
4. Reduction in Lead Times and Cost Savings
By managing inventory strategically, we help businesses reduce long lead times and lower procurement costs. Our VMI solutions minimize administrative overhead, reduce emergency orders, and eliminate excess inventory carrying costs, resulting in significant savings.
5. Compliance and Quality Assurance
In industries where component failure is not an option, quality assurance is paramount. ES Components ensures that every part supplied through VMI meets stringent industry standards, including MIL-SPEC, medical-grade, and aerospace certifications.
The Business Impact of ES Components’ VMI Program
Organizations that implement ES Components’ VMI solutions experience tangible benefits, including:
Improved Production Continuity: Eliminating stockouts ensures smooth manufacturing operations.
Lower Procurement Workload: Automating inventory replenishment reduces administrative burdens.
Better Cash Flow Management: Optimized inventory levels free up capital for other strategic investments.
Stronger Supplier Collaboration: A VMI partnership fosters transparency and efficiency across the supply chain.
Conclusion
For companies operating in aerospace, military, medical, and industrial markets, effective inventory management is essential. ES Components’ Vendor Managed Inventory (VMI) solutions provide a streamlined, cost-effective approach to maintaining critical component availability. With a focus on data-driven inventory planning, customized solutions, and a deep understanding of mission-critical supply chain demands, we empower businesses to operate with confidence and efficiency.
Partner with ES Components today to optimize your supply chain and ensure you always have the right components, precisely when you need them.
The Engineer’s Guide to Selecting the Perfect Resistor
Resistors are essential components in electronic circuits, regulating current flow and ensuring stable operation. While there are various types, thick film and thin film resistors are among the most widely used—especially in industries like aerospace, military, medical, and industrial applications. But what sets them apart? Let’s break it down.
Resistors are the backbone of electronic circuits, controlling current flow, defining voltage levels, and protecting sensitive components like MOSFETs. Choosing the right resistor is critical for performance, efficiency, and reliability. This guide breaks down resistor types, key specifications, and real-world applications so you can make informed design decisions.
Understanding Resistors: The Fundamentals
A resistor is a passive electrical component that limits current flow, causing a voltage drop across its terminals. The three primary characteristics engineers consider when selecting a resistor are:
Resistance (Ω): The opposition to current flow, determining how much voltage drops across the resistor.
Power Rating (W): The maximum power a resistor can dissipate before overheating. Common values range from 1/8 W to 1 W for standard applications, but higher power resistors are available.
Tolerance (%): The precision of the resistor's stated resistance, typically ±1%, ±5%, or ±10%.
Types of Resistors and Their Ideal Uses
Different resistor types serve different engineering needs. Here’s a breakdown of the most common ones:
1. Carbon Film Resistors
Description: Composed of a thin carbon layer over a ceramic core.
Best For: General-purpose applications in consumer electronics and audio equipment.
Advantages: Cost-effective, widely available, and sufficient for non-precision circuits.
2. Metal Film Resistors
Description: A thin metal layer provides greater precision and stability.
Best For: High-frequency circuits and precision applications.
Advantages: Low noise, high accuracy (±1% tolerance), and excellent stability over time.
3. Wirewound Resistors
Description: A resistive wire (often nichrome) wound around a core.
Best For: High-power and precision applications.
Advantages: Superior heat dissipation and high power ratings.
4. Ceramic Resistors
Description: High-temperature-resistant ceramic materials.
Best For: High-power applications like power supplies.
Advantages: Excellent thermal stability and rugged durability.
5. Variable Resistors (Potentiometers & Rheostats)
Description: Adjustable resistance for tuning circuit performance.
Best For: Volume controls, adjustable power supplies, and sensor calibration.
Advantages: Versatile, allowing real-time adjustments.
6. Surface Mount Resistors (SMD)
Description: Compact resistors designed for automated assembly on PCBs.
Best For: Modern miniaturized electronics and high-density PCB designs.
Advantages: Space-efficient and optimized for high-speed manufacturing.
Practical Engineering Applications of Resistors
Resistors play a critical role in countless circuit functions. Here’s how engineers implement them:
1. Voltage Division
Used to create reference voltages via a voltage divider circuit.
Exploits Kirchhoff’s Voltage Law to distribute voltage proportionally.
2. Current Limiting
Protects sensitive components from excessive current.
Example: A 440 Ω resistor in series with an LED ensures safe operation and longevity.
3. Pull-Up and Pull-Down Resistors
Ensures stable logic levels in digital circuits.
Essential for microcontrollers and logic gates where floating inputs can cause erratic behavior.
4. Transistor Biasing
Determines the operating point of a transistor in amplifier circuits.
Ensures consistent and predictable transistor performance.
5. Signal Filtering
Combined with capacitors to form low-pass, high-pass, and band-pass filters.
Shapes signal frequencies for applications like audio processing and RF circuits.
Conclusion
Resistors are the most fundamental components in the world of electronics. Resistors are essential for controlling the flow of current and protecting sensitive electronic components. Understanding how to use the right resistor is crucial for any and every electronics project. Whether you're an engineer, hobbyist, or tech enthusiast, a deeper understanding of these components empowers you to innovate and optimize your designs. Explore our selection of high-quality resistors from world-class manufacturer—Vishay Intertechnology,—proudly offered through ES Components. Let us help you find the perfect solution for your applications
Buy Bare Die Like a Pro: Insider Secrets Revealed
Navigating the world of Bare Die can be overwhelming if you're new to it. Unlike standard packaged semiconductors, purchasing bare die isn’t as simple as searching for a part number online. Many suppliers view it as a niche market, making it even trickier to source. However, once you understand the key differences between packaged components and bare die, you’ll be well on your way to buying like a seasoned expert.
Navigating the world of Bare Die can be overwhelming if you're new to it. Unlike standard packaged semiconductors, purchasing bare die isn’t as simple as searching for a part number online. Many suppliers view it as a niche market, making it even trickier to source. However, once you understand the key differences between packaged components and bare die, you’ll be well on your way to buying like a seasoned expert.
Step 1: Find a Trusted Bare Die Supplier
The first and most critical step is to partner with a reputable bare die supplier. A knowledgeable supplier can guide you through the complexities of the process, ensuring you get the right components with the necessary:
Certificates of Conformance
Lot Traceability
Source Control Drawings
Geometries and Specific Testing Requirements
Since not all bare die components are readily available, working with an experienced supplier will save you time, reduce risk, and prevent costly mistakes.
Step 2: Understand the Manufacturing Process
Manufacturers produce bare die by fabricating wafers, which are then tested and cut into individual die. These die are assigned part numbers before being shipped to specialized bare die distributors.
At this stage, distributors conduct Lot Acceptance Testing (LAT) to verify the quality of the die. Additional testing methods, such as Known Good Die (KGD) verification, further ensure reliability.
Step 3: Know What to Expect from Distributors
When purchasing bare die, visual inspection is critical. Experienced distributors apply military-grade inspection techniques to identify flawless die that are likely to function optimally.
However, several factors can impact availability:
Some parts may not be available in bare die form.
Minimum purchase quantities from manufacturers may exceed your needs.
Die geometries change over time, so keeping updated specifications is essential.
Working with a trusted supplier ensures you receive accurate information and, when necessary, sample die for qualification and testing.
The Industries That Rely on Bare Die
Bare die technology is the go-to solution for applications where size, performance, and reliability are paramount. Industries such as:
✔ Aerospace
✔ Military & Defense
✔ Avionics
✔ Medical Implants
✔ Automotive
✔ High-End Industrial Applications
… all depend on bare die for their cutting-edge designs.
Final Takeaway
Buying bare die doesn’t have to be intimidating. By partnering with a trusted supplier, understanding the manufacturing process, and knowing how distributors operate, you’ll be well-equipped to buy bare die like a pro.
Accelerate Your Innovation: The Future of Value-Added Solutions
In today’s fast-paced world, getting your innovations to market quickly is the key to staying ahead. But what if you had a partner that didn’t just supply components—but enhanced your entire process?
In today’s fast-paced world, getting your innovations to market quickly is the key to staying ahead. But what if you had a partner that didn’t just supply components—but enhanced your entire process?
At ES Components, we go beyond traditional distribution. Our value-added solutions are designed to optimize productivity, improve efficiency, and ensure you get exactly what you need, precisely when you need it. By prioritizing quality, customization, and attention to detail, we provide a seamless, tailored experience that helps you bring your vision to life—faster and more efficiently.
When every second counts, trust a partner who understands that the details make the difference. Experience the future of value-added solutions—because innovation shouldn’t wait.
Why Engineers Should Rely on Distributors for Component Sourcing
As an engineer, your job is to bring a concept to life. Whether you're designing a custom power supply or assembling a complex electronic system, one thing is certain—you need parts. Lots of them. But where should you source them? Should you spend hours navigating multiple manufacturer websites, or is there a better way?
As an engineer, your job is to bring a concept to life. Whether you're designing a custom power supply or assembling a complex electronic system, one thing is certain—you need parts. Lots of them. But where should you source them? Should you spend hours navigating multiple manufacturer websites, or is there a better way?
The answer is clear: partnering with a distributor simplifies and streamlines the process, making your job easier and your projects more efficient. Here’s why choosing a distributor is the smart move for engineers dealing with extensive bills of materials (BOMs):
1. One-Stop Shopping for Every Component
Think of sourcing components like ordering a meal. You wouldn’t go to separate restaurants for your burger, fries, and drink—it’s far more convenient to get everything from one place. The same applies to electronics. Distributors stock millions of parts from multiple manufacturers, giving you a single source for everything you need.
2. Efficient BOM Management
A distributor's platform provides powerful BOM tools that streamline the entire process. These tools help verify part availability, suggest alternatives, and ensure order accuracy. Instead of spending hours cross-referencing part numbers, you can make informed decisions quickly.
3. Access to Comprehensive Online Resources
Need technical specs? No problem. Distributors offer detailed datasheets, product descriptions, specifications, and application notes. Many also provide BOM management tools, conversion calculators, and search accelerator plug-ins—helping you design smarter and faster.
4. Collaborative Project & Cart Sharing
Working in a team? Many distributors allow engineers to share their projects and shopping carts with colleagues or procurement teams. This feature helps ensure that the right parts are being ordered and that everyone stays on the same page.
5. Flexible Order Quantities & Fast Shipping
Whether you need a single prototype component or a bulk order of thousands, distributors offer flexible purchasing options. Plus, with centralized sourcing, you can consolidate shipping and receive all your parts in one delivery—often with same-day processing.
6. Superior Customer Support & Technical Assistance
Forget navigating multiple customer service lines. Distributors provide dedicated technical support, online chat, and order tracking. You also gain access to historical purchase records, making reordering seamless.
7. Simplified Logistics & Cost Savings
Ordering from multiple manufacturers means juggling different shipping schedules, payment processes, and tracking numbers—not to mention paying for separate shipping fees. A distributor consolidates everything, saving you time, hassle, and money.
The Bottom Line
Time is a valuable resource, and efficiency is key in engineering. Using a distributor eliminates unnecessary complications, allowing you to focus on what really matters—bringing your project to life. So next time you're sourcing components, make the smart choice. Choose a distributor and streamline your entire process.