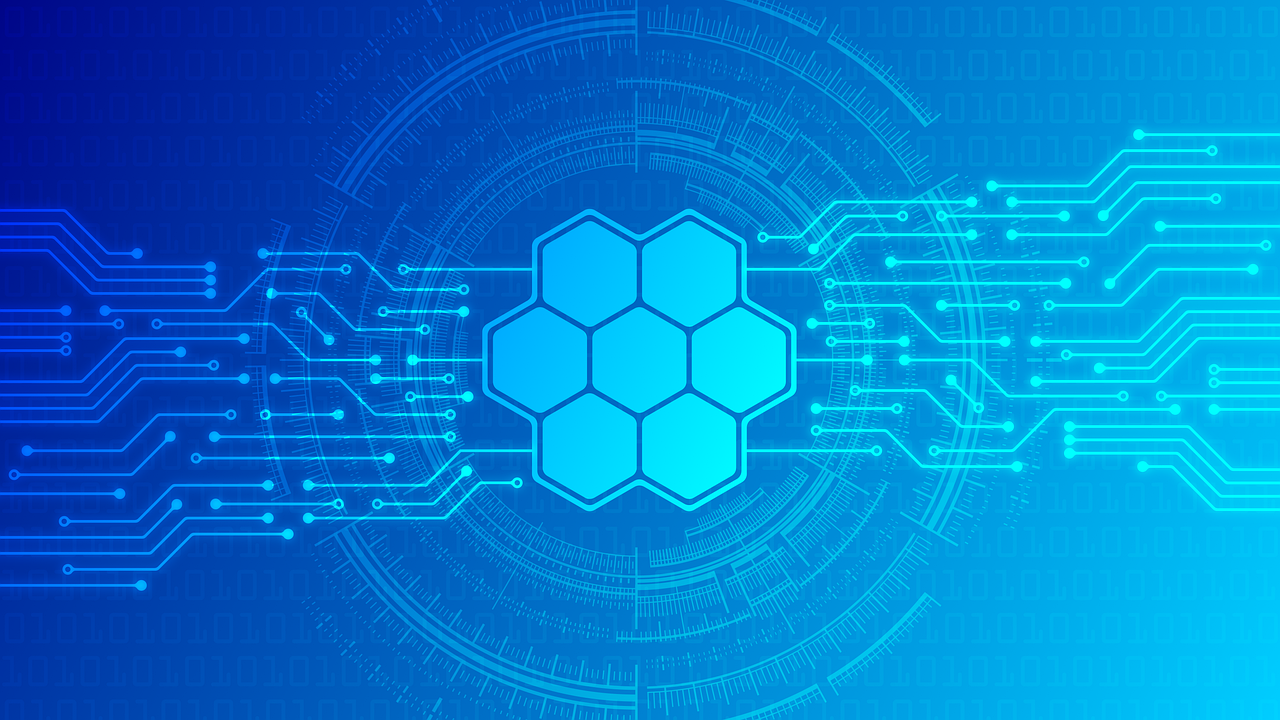
TECH TALK
High Reliability Insights From ES Components
The Official Blog of
Seal the Deal: Why Hermetic Packaging Is a Non-Negotiable for High-Reliability Electronics
In the world of advanced electronics, there's one silent killer that design engineers must constantly outwit: the environment. Moisture, gas, and contamination don’t just degrade performance—they destroy long-term reliability. That’s where hermetic packaging comes in: the unsung hero shielding your most sensitive components from failure.
In the world of advanced electronics, there's one silent killer that design engineers must constantly outwit: the environment. Moisture, gas, and contamination don’t just degrade performance—they destroy long-term reliability. That’s where hermetic packaging comes in: the unsung hero shielding your most sensitive components from failure.
🚨 Why We Need Hermetically Sealed Devices
When you're designing systems for critical missions—whether in orbit, under the hood, or inside the human body—there is zero room for failure. The smallest ingress of moisture or gas can lead to:
Corrosion of internal circuitry
Short circuits and leakage currents
Performance drift in precision devices
Total system failure in high-risk environments
Hermetically sealed devices offer a complete barrier to the external environment, ensuring consistent performance, unmatched reliability, and extended lifespan.
🔬 The Science Behind Hermetic Packaging
Hermetic packages are typically constructed from metal, ceramic, or glass-to-metal seals, materials that form an airtight enclosure around the component. Unlike plastic packaging, these materials are impermeable to moisture, oxygen, and contaminants—making them ideal for electronics that must perform flawlessly under stress.
💡 Real-World Examples of Hermetic Devices
Let’s talk about the devices that benefit from hermetic sealing, and where they’re making a critical impact:
🔹 MEMS Sensors
Used in: Airbag systems, aerospace navigation, industrial automation
Why sealed: Prevents drift and failure due to humidity or pressure variation
🔹 Optoelectronic Components (e.g., laser diodes, photodetectors)
Used in: Fiber-optic communications, lidar systems, military targeting
Why sealed: Keeps particles and moisture out of light paths to ensure optical clarity
🔹 Implantable Medical Devices
Used in: Pacemakers, neurostimulators, cochlear implants
Why sealed: Prevents body fluids from entering and maintains biocompatibility
🔹 Space-Grade Power Modules & Transistors
Used in: Satellites, space probes, defense systems
Why sealed: Protects from radiation, vacuum, and extreme thermal cycling
🔹 Crystal Oscillators & Timing Devices
Used in: GPS, avionics, communication infrastructure
Why sealed: Ensures frequency stability over decades
🏭 Industries That Demand Hermetic Solutions
Aerospace & Defense – High-reliability, mission-critical electronics
Medical & Life Sciences – Devices implanted in or used on the human body
Automotive – Advanced driver-assist systems, crash detection
Telecom – Optical networks and high-speed data transmission
Industrial & Harsh Environments – Robotics, oil & gas, and energy systems
👨💻 Final Thoughts for the Design Engineer
Hermetic packaging isn’t just a spec—it’s a strategic design decision. When you’re engineering for longevity, precision, or safety, what protects your component matters just as much as the component itself.
Whether you’re launching systems into space, installing devices inside the human body, or embedding electronics in extreme environments—hermetic packaging seals the future of your innovation.
The Invisible Force Behind Innovation: Why Design Engineers Can’t Ignore RF & Microwave Tech Anymore
Medical integrated circuits (ICs) are at the heart of modern healthcare, powering everything from implantable devices to diagnostic equipment. However, as technology advances, engineers face a growing set of challenges that demand innovative solutions. Here’s a deeper dive into the most pressing issues shaping the industry today
In today’s hyper-connected world, if your design doesn’t talk, sense, or scan, it’s already behind the curve. That’s where RF (Radio Frequency) and microwave technology step in—powering the invisible layer of communication and control in virtually every modern system.
Whether you’re building the next-gen autonomous drone or a tiny wearable heart monitor, RF and microwave components are the secret weapons driving high-performance connectivity and precision.
What Are RF & Microwave Devices?
RF and microwave devices operate in the high-frequency electromagnetic spectrum, roughly between 3 kHz and 300 GHz. These frequencies are where wireless communication, radar systems, and advanced sensing come to life.
Examples include:
Amplifiers (LNAs, PAs)
Mixers and modulators
Filters and couplers
Switches and phase shifters
Oscillators and synthesizers
Antennas and RF ICs
In short: if you need to send, receive, filter, or amplify a signal wirelessly—you're in RF land.
🏭 Who’s Using RF & Microwave—and Why?
RF isn’t just for telecom giants anymore. These devices are foundational to dozens of industries:
🚀 Aerospace & Defense
Secure comms, radar, electronic warfare, missile guidance.
Requires rugged, radiation-hardened, and high-frequency solutions.
🏥 Medical
Wireless implantable devices, RF ablation, MRI, remote monitoring.
Focused on low-power, biocompatible, and ultra-reliable designs.
🚗 Automotive & EVs
Radar for collision avoidance (77 GHz), keyless entry, V2X communications.
Needs millimeter-wave operation with low latency.
📶 Telecom & 5G
Base stations, beamforming, high-speed backhaul.
Prioritizes high-bandwidth, low-noise, and multi-channel processing.
🏭 Industrial & IoT
Remote sensors, predictive maintenance, wireless control systems.
Emphasis on range, power efficiency, and cost.
🧪 Specs That Matter
Design engineers need to get hands-on with the numbers. Here are the key specs to compare when picking RF/microwave components:
Parameter What It Means
· Frequency Range Defines usable spectrum (e.g. 2.4 GHz, 77 GHz)
· Gain / Noise Figure Amplification vs. signal clarity—balance both
· Linearity (IP3/P1dB) Handles strong signals without distortion
· VSWR / Return Loss Ensures efficient power transfer, reduces reflection
· Phase Noise / Jitter Crucial for oscillator precision in comms/radar
· Insertion Loss Signal loss across a device (especially in filters)
· Power Handling Max power capability (important for transmitters)
💰 Are RF Devices Cost-Effective?
Absolutely—but it depends on your design priorities:
Mass-market wireless (Wi-Fi, Bluetooth, Zigbee): Extremely cost-effective thanks to scale and integrated RF SoCs.
High-performance applications (mil-aero, radar, medical): Pricier, but justified by unmatched performance, customization, and reliability.
Miniaturized RF modules: Offer plug-and-play solutions that save dev time and reduce PCB complexity.
The key is choosing the right component for your system architecture. Sometimes a smart RF front end can replace multiple discrete components, actually lowering BOM cost and power draw.
🛠️ Final Thoughts: RF Isn’t Optional Anymore
We’re in an era where "wireless by default" is the expectation. Whether it’s:
Sensing traffic patterns
Monitoring vitals remotely
Communicating between drones
Or directing energy in an advanced radar system
RF and microwave devices are what make it possible.
For design engineers, mastering this domain doesn’t just unlock new possibilities—it puts you ahead of the curve in industries racing to innovate.
Unlock the Future: Why Every Design Engineer Should Be Thinking FPGA Right Now
f you're still leaning on microcontrollers and CPUs for all your embedded designs, it might be time to rethink. Enter the Field-Programmable Gate Array—better known as the FPGA—the ultimate tool for engineers who want raw performance, precision, and customization in their corner.
If you're still leaning on microcontrollers and CPUs for all your embedded designs, it might be time to rethink. Enter the Field-Programmable Gate Array—better known as the FPGA—the ultimate tool for engineers who want raw performance, precision, and customization in their corner.
So, what is an FPGA, really? Why are industries from aerospace to AI going all-in on them? And most importantly, are they worth the cost?
Let’s break it down.
🧠 What is an FPGA, Really?
At its core, an FPGA is a blank slate of logic gates—ANDs, ORs, flip-flops, multiplexers—just waiting to be configured. You use a hardware description language (HDL) like Verilog or VHDL to build custom digital circuits directly into silicon.
Think of it like this:
A CPU follows instructions, one at a time.
A microcontroller juggles a few tasks with some real-world interfacing.
But an FPGA? You build the machine that runs the task. Parallel. Precise. Custom.
⚙️ Specs That Matter
FPGAs come in a wide range of flavors—from entry-level boards to ultra-high-performance monsters. Here's what typically matters:
Logic Elements (LEs): These are your basic building blocks. More LEs = more complex designs.
DSP Slices: For multiply-accumulate operations—key for AI, audio, video, and signal processing.
Block RAM: Embedded memory for fast, local access.
I/O Flexibility: From LVDS to PCIe, FPGAs handle almost any protocol.
Clocking and PLLs: Get precise timing control down to nanoseconds.
On-chip Processors: Many FPGAs now include embedded ARM cores (hello, Xilinx Zynq).
🌎 Who Should Be Using FPGAs?
If your design needs:
Real-time performance
Massive data throughput
Unique interface protocols
Hardware-level security
Upgradability without re-spinning silicon
Then you should seriously be considering FPGAs.
Industries leading the way include:
Aerospace & Defense: Secure, mission-critical systems with extreme timing needs.
Medical Devices: Imaging, diagnostics, and robotic surgical systems.
Automotive: Real-time decision making in autonomous systems.
Industrial Automation: Custom machine control and edge processing.
Telecom & 5G: High-speed packet processing and modulation.
💰 Are FPGAs Cost-Effective?
They used to be expensive. Now? It depends on your priorities.
For low-volume, high-performance designs, FPGAs beat the cost and time of a custom ASIC every time.
For prototypes, you can iterate in hardware before you commit to silicon.
For production, many mid-range FPGAs now compete on price with high-end MCUs—especially when you factor in the savings on external components (because the FPGA can absorb them!).
Also worth noting: FPGAs are getting more developer-friendly. Tools like Xilinx Vitis and Intel Quartus now offer HLS (High-Level Synthesis) that let you write in C/C++ instead of HDL.
🚀 Final Word: FPGAs Are No Longer Niche
This isn’t a tool just for hardcore hardware engineers anymore. If you're a design engineer pushing boundaries in performance, flexibility, or precision, FPGAs should be in your toolkit—no question.
You don’t need to replace everything. But the moment you do your first real-time image processor or custom motor controller on an FPGA and watch it hum at full speed with nanosecond accuracy?
You’ll never look at a microcontroller the same way again.
Why High-Reliability Electronic Components Are a Must for Critical Applications
When failure isn’t an option, standard commercial components just don’t cut it. Whether you're designing for the skies, the battlefield, or a medical implant, your systems need to perform flawlessly under pressure. That’s where High-Reliability (Hi-Rel) electronic components come into play.
Top Reasons, Key Industries, and Product Types That Demand Zero-Failure Performance
When failure isn’t an option, standard commercial components just don’t cut it. Whether you're designing for the skies, the battlefield, or a medical implant, your systems need to perform flawlessly under pressure. That’s where High-Reliability (Hi-Rel) electronic components come into play.
In this post, we’ll break down why Hi-Rel components are essential, which industries absolutely depend on them, and the key product types design engineers should consider.
5 Reasons Why Design Engineers Should Use Hi-Rel Components
1. Built for Extreme Environments
Hi-Rel components are engineered to function in the most demanding conditions—intense heat, cold, vibration, shock, and even radiation. They're ideal for aerospace, automotive, and other mission-critical applications.
2. Unmatched Reliability
These components go through rigorous screening and testing like burn-in, thermal cycling, and mechanical stress. This significantly reduces early-life and random failures—keeping your system running without surprises.
3. Longer Product Lifecycles
Systems in aerospace, defense, or medical fields often need to last decades. Hi-Rel components are built for the long haul, reducing replacement needs and maintenance costs over time.
4. Safety and Compliance
Meeting strict industry standards (MIL-STD, ISO, IPC) is often mandatory. Hi-Rel parts help meet these safety and quality benchmarks—boosting both your credibility and product certification success.
5. Lower Total Cost of Ownership
While Hi-Rel parts may cost more up front, they save money over time by reducing costly downtime, repairs, recalls, and warranty claims—especially in systems where failure can be catastrophic.
🌍 Industries That Count on High-Reliability Components
✈️ Aerospace & Defense
From satellites and radar systems to missile guidance and avionics—these systems operate in extreme conditions where failure isn’t just inconvenient, it’s mission-critical. Hi-Rel components ensure consistent, rugged performance.
🏥 Medical Devices
Life-saving devices like pacemakers, defibrillators, and surgical systems need zero-failure performance. Hi-Rel parts meet the strict reliability and sterilization standards required by the medical field.
🚗 Automotive (EVs & ADAS)
Today’s vehicles are complex, computer-driven machines. Electric vehicles (EVs), battery management systems, and ADAS features require components that can withstand heat, vibration, and 24/7 operation.
🏭 Industrial & Robotics
Industrial automation and robotics operate in high-stress environments—often around the clock. Hi-Rel parts help maintain uptime and prevent costly production halts.
⛽ Energy, Oil & Gas
Exploration and drilling systems operate in remote and punishing environments. Hi-Rel electronics are a must for consistent, long-life performance in places you can’t afford to fail.
📡 Telecommunications & Space
From space-based data links to satellite ground stations, communication systems need components that can handle radiation, temperature extremes, and long mission durations without fail.
🧩 Common Hi-Rel Electronic Component Types
🔌 Semiconductors
Power MOSFETs
Bipolar Junction Transistors (BJTs)
Diodes, Rectifiers, Voltage Regulators
Radiation-hardened Microcontrollers
Power Management ICs
🔋 Passive Components
Tantalum & Ceramic Capacitors
Precision Resistors
Inductors & Magnetics
🧠 Memory & Logic
Radiation-hardened EEPROM / Flash
SRAMs and FPGAs for space and defense applications
📦 Interconnect & Packaging
Hermetic packages
MIL-STD connectors
Hybrid assemblies and custom modules
📡 RF & Microwave
High-frequency amplifiers
Oscillators and filters
RF switches and mixers
Final Thoughts
For design engineers working in high-stakes industries, Hi-Rel components aren't a luxury—they're a necessity. The right components not only improve system performance and longevity, but they also protect your reputation and bottom line.
Avoiding Common Capacitor Mishaps: Why Passive Component Selection Matters More Than You Think
Avoiding Common Capacitor Mishaps: Why Passive Component Selection Matters More Than You Think. It’s easy to underestimate their impact, but capacitor selection and sourcing can make or break a design. Here’s why this often-overlooked stage deserves more attention.
When it comes to circuit design, especially in printed circuit board (PCB) development, much of the spotlight shines on active components like processors, memory, and specialized ICs. But tucked away in the corners of every board are unsung heroes: discrete passive components—resistors, inductors, and yes, capacitors.
It’s easy to underestimate their impact, but capacitor selection and sourcing can make or break a design. Here’s why this often-overlooked stage deserves more attention.
1. The Illusion of Simplicity
Capacitors are frequently seen as basic building blocks—commodities that can be plugged in with little thought. But that assumption hides a complex reality. Critical specs like:
Capacitance tolerance
Dielectric material (e.g., X7R, NP0, Y5V)
ESR (Equivalent Series Resistance)
Voltage rating
...can drastically affect circuit performance, especially in power delivery networks, signal filtering, or high-frequency designs. Selecting the wrong type can lead to instability, noise, or premature failure.
2. Relying on Default BOMs or Library Parts
Designers working within CAD tools often default to components from standard libraries or past projects. While this saves time upfront, it can lead to big headaches later when a selected capacitor turns out to be:
Obsolete (EOL)
On allocation with 52-week lead times
Incompatible with regulatory or reliability specs
Proactive sourcing—ensuring the component is available, qualified, and future-proof—is essential for avoiding redesigns and delays.
3. The Supply Chain Isn’t What It Used to Be
Once upon a time, capacitors were “always in stock.” Not anymore.
In today’s tight and volatile supply chain environment, even the most common capacitor values may become hard to source. And with certain dielectrics or temperature ratings in high demand, early coordination with sourcing teams or reliable distributors can save your project from production stalls.
4. Performance on the PCB Isn’t Just About Specs
On the datasheet, a capacitor may look perfect—but on your PCB, layout choices matter just as much. Factors like:
Trace and via parasitics
Proximity to power pins
Stack-up and ground return paths
…affect real-world performance, especially for decoupling, filtering, or noise suppression. A poorly placed or selected capacitor can lead to EMI, ringing, or power integrity issues that are hard to debug and expensive to fix.
5. Special Requirements? Special Considerations
In mission-critical applications—think aerospace, medical, automotive, or industrial—capacitors must meet:
MIL-spec or AEC-Q200 standards
Wide temperature tolerances
Hermetic sealing or screening
Designers who skip over these requirements during the selection phase risk non-compliance, test failures, or in-field reliability issues.
Key Takeaways
Capacitors might seem like simple components, but they carry serious design weight. To avoid costly mishaps:
+ Don’t treat passives as interchangeable commodities
+ Coordinate with sourcing teams early
+ Match component specs to real-world performance needs
+ Plan for long-term availability and compliance
By giving capacitors—and other passives—the attention they deserve during the selection and sourcing process, you can elevate the reliability and success of your entire PCB design.
MOSFETs: The Powerhouse Behind Modern Electronics
Medical integrated circuits (ICs) are at the heart of modern healthcare, powering everything from implantable devices to diagnostic equipment. However, as technology advances, engineers face a growing set of challenges that demand innovative solutions. Here’s a deeper dive into the most pressing issues shaping the industry today
The metal–oxide–semiconductor field-effect transistor (MOSFET) is a cornerstone of modern electronics. Invented by Mohamed Atalla and Dawon Kahng at Bell Labs in 1959, the MOSFET has become the most widely used transistor in the world — a vital component in everything from microprocessors to power circuits.
MOSFET: The Transistor That Drives Modern Technology
The metal–oxide–semiconductor field-effect transistor (MOSFET) is a cornerstone of modern electronics. Invented by Mohamed Atalla and Dawon Kahng at Bell Labs in 1959, the MOSFET has become the most widely used transistor in the world — a vital component in everything from microprocessors to power circuits.
How Does a MOSFET Work?
A MOSFET is a type of field-effect transistor (FET) that controls electrical conductivity based on the voltage applied to its insulated gate. By adjusting this voltage, engineers can amplify or switch electronic signals with remarkable efficiency.
Why Engineers Rely on MOSFETs
MOSFETs offer several key advantages that have made them indispensable in electronics design:
Minimal Power Consumption: Unlike bipolar junction transistors (BJTs), MOSFETs require very little input current to control large output currents.
Flexible Operation Modes:
Enhancement Mode: Voltage at the gate enhances conductivity.
Depletion Mode: Voltage at the gate reduces conductivity.
Scalability and Efficiency: MOSFETs are easily miniaturized, following Moore's Law for increased density and performance.
Cost-Effective Manufacturing: Simpler processing steps and high yield make MOSFETs affordable and widely available.
Real-World Impact
Power MOSFETs, often found in surface-mount packages, are capable of handling substantial power loads. For example, MOSFETs in D2PAK packages can block voltages up to 120V, conduct 30A continuously, and manage power loads exceeding 2000W — all while dissipating minimal heat.
The Backbone of Digital Innovation
MOSFETs are the foundation of digital electronics. Found in everything from smartphones and computers to industrial equipment, billions of MOSFETs are produced daily. The technology’s scalability and low power requirements have fueled advancements in integrated circuits (ICs) and very large-scale integration (VLSI) devices.
The U.S. Patent and Trademark Office recognizes the MOSFET as a “groundbreaking invention that transformed life and culture around the world.” Its influence continues to shape modern electronics, ensuring innovation for decades to come.
Integrated Circuits: The Brains Behind Modern Electronics
Integrated Circuits (ICs), or microchips, are the backbone of modern electronics, enabling everything from smartphones to aerospace systems. By packing thousands—or even billions—of transistors onto a single semiconductor chip, ICs deliver high performance, efficiency, and reliability in a compact form.
Integrated Circuits (ICs), or microchips, are the backbone of modern electronics, enabling everything from smartphones to aerospace systems. By packing thousands—or even billions—of transistors onto a single semiconductor chip, ICs deliver high performance, efficiency, and reliability in a compact form.
What Are Integrated Circuits?
ICs are miniature electronic circuits etched onto semiconductor material, typically silicon. They house essential components like transistors, diodes, resistors, and capacitors, all intricately connected to execute specific functions.
How Do ICs Work?
ICs function by directing electrical signals through complex networks of interconnected components. Depending on their design, they can process data, amplify signals, regulate power, or manage communications.
Types of Integrated Circuits
Engineers categorize ICs based on their signal processing capabilities:
Digital ICs: Handle binary signals (on/off), forming the foundation of microprocessors, logic gates, and memory chips.
Analog ICs: Process continuous signals for applications like audio amplification and sensor data interpretation.
Mixed-Signal ICs: Integrate both digital and analog functions, commonly found in communication systems and embedded electronics.
Key Functions of ICs
ICs serve a vast range of applications, including:
Logic and Computation: Powering processors, controllers, and memory modules.
Signal Processing: Amplifying, filtering, and converting signals in audio, RF, and sensor applications.
Power Management: Regulating voltage, converting power efficiently, and optimizing energy consumption.
Common IC Applications
ICs are integral to numerous devices, including:
Microprocessors: The core of computers, mobile devices, and embedded systems.
Memory Chips: Storing data for everything from PCs to IoT devices.
Sensors: Converting real-world inputs into digital data for automation and monitoring.
Audio Amplifiers: Enhancing sound quality in consumer and professional audio equipment.
Why ICs Are Essential
ICs revolutionized electronics by offering:
Miniaturization: Shrinking complex circuits into tiny chips.
High-Speed Performance: Enabling rapid data processing and communication.
Energy Efficiency: Reducing power consumption in portable and industrial applications.
Cost-Effectiveness: Mass production lowers manufacturing costs while improving reliability.
Final Thoughts
From aerospace and medical devices to smartphones and industrial automation, integrated circuits are at the heart of technological advancement. As semiconductor technology continues to evolve, ICs are becoming more powerful, efficient, and indispensable in engineering innovations.
Key Challenges in Medical Integrated Circuits Today
Medical integrated circuits (ICs) are at the heart of modern healthcare, powering everything from implantable devices to diagnostic equipment. However, as technology advances, engineers face a growing set of challenges that demand innovative solutions. Here’s a deeper dive into the most pressing issues shaping the industry today
Medical integrated circuits (ICs) are at the heart of modern healthcare, powering everything from implantable devices to diagnostic equipment. However, as technology advances, engineers face a growing set of challenges that demand innovative solutions. Here’s a deeper dive into the most pressing issues shaping the industry today.
1. Regulatory Compliance and Quality Assurance: The High-Stakes Barrier
Unlike consumer electronics, medical ICs must meet stringent regulatory standards such as FDA, ISO 13485, and IEC 60601. Compliance isn’t just a checkbox—it requires rigorous design validation, traceability, and testing protocols. Any failure can delay product launches or even lead to costly recalls.
2. Cybersecurity: The Hidden Threat in Connected Devices
With the rise of wireless and IoT-enabled medical devices, cybersecurity is a growing concern. Pacemakers, insulin pumps, and hospital equipment are now potential targets for cyberattacks. Engineers must implement robust encryption, authentication, and real-time monitoring to ensure both patient safety and data integrity.
3. Supply Chain Disruptions: Securing a Stable Component Pipeline
Global semiconductor shortages, geopolitical tensions, and reliance on a handful of suppliers make sourcing high-reliability components a challenge. Engineers must design with supply chain resilience in mind—finding second-source components, using adaptable architectures, and considering longevity in part availability.
4. Power Efficiency & Thermal Management: The Ultimate Balancing Act
Medical ICs, especially for implantable and wearable devices, must deliver high performance with ultra-low power consumption. Managing heat dissipation in a tiny package is another challenge—excess heat can damage tissue or degrade sensor accuracy. Innovations in power management ICs (PMICs) and energy harvesting solutions are key to overcoming these limitations.
5. Patient Safety: Designing for Zero Failure
Reliability isn’t optional in medical electronics—lives depend on it. Engineers must ensure fail-safe designs, redundancy mechanisms, and extensive testing under real-world conditions. Radiation exposure, biocompatibility, and electromagnetic interference (EMI) all add layers of complexity to the development process.
6. The Ever-Changing Regulatory Landscape
As medical technology evolves, so do the regulations. Engineers must stay ahead of shifting global standards, from cybersecurity mandates to new approval pathways for AI-driven medical devices. Agility in adapting to regulatory changes is critical for bringing products to market.
7. Industrial Design Meets Engineering: Sterilization & Durability Challenges
Medical ICs often need to function in extreme conditions—exposed to repeated sterilization cycles, fluids, and harsh disinfectants. Designing circuits that withstand these environments without degradation is a tough materials-science challenge, requiring innovation in encapsulation, coatings, and hermetic sealing.
8. Intellectual Property & Counterfeit Risks
Counterfeit ICs are a growing problem in high-reliability sectors, including medical devices. Engineers and manufacturers must implement robust sourcing strategies, authentication methods, and supply chain tracking to prevent compromised components from entering critical applications.
9. Mixed-Signal IC Design: Where Analog Meets Digital Complexity
Many medical ICs operate in mixed-signal environments, requiring precision analog circuitry alongside high-speed digital processing. Challenges such as noise mitigation, power efficiency, clock distribution, and signal integrity require sophisticated design techniques and specialized tools.
10. Physical Defects: The Hidden Enemies of Reliability
Medical ICs must withstand long-term operation without failure. Common failure mechanisms include:
Gate-Oxide-Shorts and TDDB (Time-Dependent Dielectric Breakdown), which degrade transistor performance.
ESD (Electrostatic Discharge), which can destroy delicate circuitry.
Electric Field Stress, leading to unexpected degradation over time.
Reliability testing, robust packaging, and defect mitigation strategies are essential to extend device lifespan.
Conclusion: Engineering the Future of Medical ICs
As medical technology continues to evolve, engineers are at the forefront of solving these complex challenges. From designing ultra-low-power chips to securing devices against cyber threats, the next generation of medical ICs will require innovation, adaptability, and precision. The future of healthcare depends on the ability to push these boundaries—while ensuring safety, reliability, and compliance every step of the way.
Why Aerospace Customers Rely on High-Reliability Microelectronic Components
In the aerospace industry, reliability isn’t just a priority—it’s a necessity. Aerospace systems operate in some of the harshest environments imaginable, where even the smallest electronic failure can lead to catastrophic consequences. That’s why high-reliability (hi-rel) microelectronic components are the backbone of mission-critical aerospace applications.
In the aerospace industry, reliability isn’t just a priority—it’s a necessity. Aerospace systems operate in some of the harshest environments imaginable, where even the smallest electronic failure can lead to catastrophic consequences. That’s why high-reliability (hi-rel) microelectronic components are the backbone of mission-critical aerospace applications.
Why Reliability Matters
1. Extreme Environments
From the searing heat of reentry to the freezing void of space, aerospace electronics must endure extreme temperatures, intense vibrations, radiation exposure, and relentless mechanical stress. Ordinary components simply won’t survive.
2. Mission-Critical Operations
Failure is not an option in aerospace. Whether controlling an aircraft’s flight systems, powering a satellite’s communications, or navigating a deep-space probe, these components must function flawlessly—every time. A single failure could mean loss of life, mission failure, or millions of dollars in damages.
3. Longevity & Durability
Unlike consumer electronics, aerospace components must last for decades without failure. Satellites, aircraft, and spacecraft are expected to perform reliably over extended lifetimes, often in environments where maintenance is impossible.
4. Performance at the Highest Level
Aerospace applications demand precision, speed, and efficiency. Hi-rel microelectronics provide the power and processing capabilities required for cutting-edge avionics, satellite communications, and advanced guidance systems.
5. Safety & Security
Passenger safety, crew security, and mission success all depend on the integrity of these components. Every electronic system must be fail-safe, resilient, and protected against external threats, including electromagnetic interference and environmental hazards.
6. Meeting Stringent Industry Standards
Aerospace electronics must comply with rigorous military and industry standards, such as MIL-STD-883 and MIL-PRF-38534, ensuring they meet the highest levels of quality, reliability, and durability.
Key High-Reliability Components
1. Semiconductors
Critical components like transistors, diodes, and integrated circuits are engineered to function under extreme conditions while maintaining optimal performance.
2. Passive Components
High-reliability resistors, capacitors, and inductors ensure stable electrical performance in aerospace systems.
3. Connectors & Cables
Built to withstand extreme temperatures, vibrations, and radiation, aerospace-grade connectors and cables provide secure and uninterrupted connections.
4. Advanced Packaging
Hermetic ceramic packaging enhances durability by protecting components from radiation, heat, outgassing, and mechanical shock.
Where Hi-Rel Microelectronics Are Used
Avionics: Flight control, navigation, and communication systems
Satellites: Power distribution, sensors, and communication modules
Spacecraft: Propulsion systems, life support, and scientific instruments
Aircraft: Engine controls, landing gear, and onboard electronics
ES Components: Your Partner in High-Reliability Solutions
At ES Components, we specialize in supplying high-reliability microelectronic components tailored for aerospace, defense, and other demanding industries. Our extensive range includes semiconductors, integrated circuits, and passive components that meet stringent industry standards. With a commitment to innovation and quality, we provide tailored solutions that ensure long-term reliability and performance in even the most extreme environments.
When failure is not an option, ES Components delivers.
Why Customers Choose Microchip Technology’s SIlicon Carbide (SiC) Products
When performance, efficiency, and reliability matter most, Microchip Technology's Silicon Carbide (SiC) solutions stand out. Designed for high-power applications, our SiC products deliver unmatched efficiency, faster switching speeds, and resilience in extreme conditions—all leading to smaller, lighter, and more reliable systems.
When performance, efficiency, and reliability matter most, Microchip Technology's Silicon Carbide (SiC) solutions stand out. Designed for high-power applications, our SiC products deliver unmatched efficiency, faster switching speeds, and resilience in extreme conditions—all leading to smaller, lighter, and more reliable systems.
Key Benefits of SiC Technology:
Unmatched Efficiency – SiC devices slash energy losses compared to traditional silicon, making them perfect for power-hungry applications while cutting operational costs.
Superior Thermal Management – Built to thrive in extreme heat, SiC ensures stable performance in demanding environments where thermal stability is critical.
Lightning-Fast Switching Speeds – Process high power levels at unprecedented speeds, optimizing high-frequency applications for superior performance.
Extreme Voltage & Current Handling – Designed to endure higher voltages, currents, and temperatures, SiC technology excels in high-demand applications.
Rugged & Reliable – With robust avalanche performance, SiC components withstand sudden power surges, preventing failures and enhancing system durability.
Smaller, Lighter Designs – Higher power density enables compact, lightweight systems, a game-changer for electric vehicles, solar inverters, and aerospace applications.
Extended EV Range – SiC boosts electric vehicle efficiency, extending range by over 7%, giving automakers a competitive edge.
Where SiC Technology is Powering the Future
🔹 Electric Vehicles – Driving greater efficiency and longer range
🔹 Solar Inverters – Maximizing energy conversion for sustainable power
🔹 Industrial Motor Drives – Enhancing performance and reliability
🔹 Residential Heat Pumps – Enabling more efficient, cost-effective home heating
Microchip: Your Partner in SiC Innovation
As a leader in SiC technology, Microchip provides a robust product portfolio and intuitive development tools to help customers design best-in-class power solutions. Whether you're building the future of EVs, renewable energy, or industrial automation, Microchip’s SiC solutions give you the competitive edge.
Ready to Upgrade? ES Components Has Microchip SiC In Stock!
At ES Components, we understand that quality, availability, and support are just as important as performance. That’s why we proudly stock Microchip SiC Bare Die, ready to ship when you need them.
🔹 Reliable Supply Chain – Avoid long lead times with our ready-to-ship inventory
🔹 Made in the USA – Ensuring top-tier quality and compliance with industry standards
🔹 Trusted Partner – Supporting aerospace, military, medical, and industrial markets
📦 Contact ES Components now to secure your Microchip SiC components!
What Are Electrolytic and Ceramic Capacitors?
Electrolytic and ceramic capacitors are two common types of capacitors, each with distinct characteristics and applications.
Electrolytic and ceramic capacitors are two common types of capacitors, each with distinct characteristics and applications.
Electrolytic Capacitors
Construction: Made with an electrolyte (a liquid or gel substance) as one of the electrodes, allowing for higher capacitance values.
Polarity: Typically polarized, meaning they have a positive and negative terminal and must be connected correctly in a circuit.
Capacitance Range: Usually ranges from 1µF to several thousand µF.
Voltage Ratings: Typically from a few volts to a few hundred volts.
Applications: Used in power supply filtering, energy storage, and signal coupling in audio and power circuits.
Types:
Aluminum Electrolytic – Most common, used in power applications.
Tantalum Electrolytic – More stable and compact but expensive.
Ceramic Capacitors
Construction: Uses a ceramic dielectric material with metal plates on either side.
Polarity: Non-polarized, so they can be connected in any direction.
Capacitance Range: Typically pF (picofarads) to low µF range.
Voltage Ratings: Can range from a few volts to several kV.
Applications: Used in high-frequency circuits, filtering, decoupling, and timing applications.
Types:
MLCC (Multilayer Ceramic Capacitors) – Common in surface-mount applications.
Disc Ceramic – Used in general-purpose applications.
Key Differences
For aerospace and military applications, capacitors must meet stringent requirements for reliability, temperature tolerance, and durability under extreme conditions. Below are recommendations for both electrolytic and ceramic capacitors suitable for these environments:
1. Electrolytic Capacitors (High-Reliability Applications)
Electrolytic capacitors are often used in power supplies, filtering, and energy storage where high capacitance is required.
Recommended Types:
Tantalum Capacitors (Mil-Spec)
Example: MIL-PRF-55365-compliant solid tantalum capacitors
Pros: Excellent stability, low ESR (Equivalent Series Resistance), long lifespan.
Cons: Sensitive to voltage spikes, more expensive.
Applications: Avionics power circuits, radar systems, mission-critical electronics.
Hermetically Sealed Aluminum Electrolytic Capacitors
Example: MIL-PRF-39018 or MIL-PRF-49470
Pros: High capacitance, ruggedized for harsh conditions.
Cons: Larger size, lower lifespan than tantalum.
Applications: Military-grade power filtering, bulk energy storage in aerospace electronics.
2. Ceramic Capacitors (High-Frequency & Temperature-Stable Applications)
Ceramic capacitors are ideal for high-frequency filtering, decoupling, and RF/microwave applications due to their low loss and stability.
Recommended Types:
High-Reliability MLCCs (Multilayer Ceramic Capacitors)
Example: MIL-PRF-123 or MIL-PRF-55681 qualified MLCCs
Pros: Excellent stability, high reliability, wide temperature range (-55°C to +200°C).
Cons: Lower capacitance compared to electrolytic.
Applications: RF communications, missile guidance systems, avionics.
Radial Leaded or Stack Capacitors
Example: High-voltage MLCCs for radar and power systems
Pros: Withstands extreme conditions, radiation-hardened variants available.
Applications: Satellite electronics, pulse power circuits in military defense systems.
Key Selection Factors for Aerospace/Military Use:
Temperature Tolerance – Components should operate reliably in extreme environments (-55°C to +125°C or higher).
Shock & Vibration Resistance – MIL-spec capacitors should meet MIL-STD-202 testing for ruggedness.
Radiation Hardening – Essential for space applications to prevent degradation from cosmic radiation.
Low ESR/ESL – Critical for high-frequency filtering in radar, avionics, and RF applications.
Vishay offers a comprehensive range of capacitors tailored for aerospace and military applications, ensuring high reliability and performance under stringent conditions. Below are specific recommendations for both electrolytic and ceramic capacitors:
1. Electrolytic Capacitors
a. STH SuperTan® Wet Tantalum Capacitors
Features:
Enhanced performance with military H-level shock (500 g) and vibration capabilities (sine: 80g; random: 54 g).
Hermetic glass-to-metal seals for improved reliability.
Suitable for avionics and aerospace applications requiring high capacitance and energy density.
Applications:
Ideal for use in avionics, aerospace, and defense systems where robust performance is critical.
Additional Information:
These capacitors are designed to withstand harsh environmental conditions, making them suitable for mission-critical applications.
b. High-Reliability Aluminum Electrolytic Capacitors
Features:
Designed for military and aerospace applications with extended operational life and stability.
Available in various configurations, including axial and radial leaded, to accommodate different design requirements.
Applications:
Used in power supplies, energy storage, and filtering applications within military and aerospace systems.
Additional Information:
These capacitors comply with military specifications, ensuring reliability in critical operations.
2. Ceramic Capacitors
a. MIL-PRF-123 Qualified Multilayer Ceramic Chip Capacitors
Features:
Space-level reliability with military qualification.
Suitable for applications requiring high performance and reliability under extreme conditions.
Applications:
Ideal for use in space systems, satellite communications, and military avionics.
Additional Information:
These capacitors are designed to meet stringent military standards, ensuring optimal performance in critical applications.
b. CDR Series (MIL-PRF-55681) Multilayer Ceramic Capacitors
Features:
Compliant with MIL-PRF-55681 standards, ensuring high reliability.
Available in various case sizes and voltage ratings to suit diverse application needs.
Applications:
Commonly used in military communication equipment, radar systems, and aerospace controls.
Additional Information:
These capacitors offer stable performance across a wide temperature range, making them suitable for harsh environments.
Key Selection Factors:
Compliance with Military Standards: Ensure capacitors meet relevant MIL specifications (e.g., MIL-PRF-123, MIL-PRF-55681) for reliability.
Environmental Tolerance: Select capacitors capable of withstanding extreme temperatures, shock, and vibration.
Electrical Performance: Consider capacitance stability, equivalent series resistance (ESR), and voltage ratings appropriate for the application.
Need a trusted partner for Electrolytic or Ceramic Capacitors? Contact us today and let’s solve obsolescence together.
Solving DMSMS Challenges with ES Components: Your Trusted Source for Vishay Siliconix Hermetic Semiconductors
Whether you're facing component obsolescence, supply chain disruptions, or custom design challenges, our expertise ensures that your critical systems remain operational, reliable, and up to specification for years to come.
Whether you're facing component obsolescence, supply chain disruptions, or custom design challenges, you want your critical systems to remain operational, reliable, and up to specification for years to come.
When it comes to DMSMS (Diminishing Manufacturing Sources and Material Shortages) solutions, ES Components stands out as a trusted partner, providing precision-engineered, high-reliability, and fully compliant semiconductor solutions. We specialize in sourcing, manufacturing, and custom packaging components that meet the stringent requirements of aerospace, military, medical, and industrial markets—industries where performance and longevity are non-negotiable. Whether you're facing component obsolescence, supply chain disruptions, or custom design challenges, our expertise ensures that your critical systems remain operational, reliable, and up to specification for years to come. At ES Components, we don’t just supply parts—we engineer solutions that bridge the gap between legacy technology and modern demands, keeping your projects on track and mission-ready.
Why ES Components?
At ES Components, we specialize in legacy and custom semiconductor solutions with a focus on precision, compliance, and reliability. Whether you need hermetic Vishay Siliconix components, custom ASIC solutions, or secure supply chain assurance, we have you covered.
10 Reasons Engineers Choose ES Components
1️⃣ MILSPEC Experts – We understand MIL-PRF-38535 & MIL-PRF-19500 and ensure compliance the first time, every time.
2️⃣ DLA-Certified Manufacturer – Our ESC brand supports DLA products and custom packaging.
3️⃣ Siliconix Hermetic Solutions – Continued source for critical military-grade semiconductors.
4️⃣ Unmatched Legacy Die Inventory – The world’s largest stock with full chain-of-custody documentation.
5️⃣ Custom Hermetic Packaging – Tailored solutions that meet MILSPEC or SCD requirements.
6️⃣ ASIC & Rad-Hard Solutions – Custom and functional equivalents (LT1009, LM158, etc.) available.
7️⃣ DMSMS Experts Since 1981 – Over 40 years of experience solving obsolescence issues.
8️⃣ Counterfeit Avoidance Commitment – Element Evaluation capabilities ensure authenticity.
9️⃣ Woman-Owned Small Business – A trusted, agile partner with a focus on quality.
🔟 Certified & Compliant – QSLD, ISO9001:2015, AS9120:2016, ITAR, GIDEP, and more.
Partner with ES Components for Your Semiconductor Needs
In mission-critical applications, failure is not an option. ES Components provides engineered solutions that ensure long-term availability, compliance, and security.
Need a trusted partner for legacy or custom semiconductor solutions? Contact us today and let’s solve obsolescence together.
Streamlining Supply Chains: How ES Components Optimizes Vendor Managed Inventory (VMI) for Mission-Critical Industries
In industries where precision, reliability, and efficiency are critical—such as aerospace, military, medical, and industrial manufacturing—effective supply chain management can mean the difference between operational success and costly delays. Vendor Managed Inventory (VMI) is a powerful solution that ensures businesses have the right components when they need them, reducing lead times, minimizing stockouts, and optimizing inventory levels.
In industries where precision, reliability, and efficiency are critical—such as aerospace, military, medical, and industrial manufacturing—effective supply chain management can mean the difference between operational success and costly delays. Vendor Managed Inventory (VMI) is a powerful solution that ensures businesses have the right components when they need them, reducing lead times, minimizing stockouts, and optimizing inventory levels.
ES Components specializes in VMI solutions tailored to the unique demands of these mission-critical industries, offering expertise and strategic inventory management that helps businesses stay ahead.
What is Vendor Managed Inventory (VMI)?
Vendor Managed Inventory (VMI) is a supply chain strategy where a supplier takes responsibility for maintaining an agreed inventory level at the customer's facility or a designated warehouse. Instead of traditional inventory management, where the customer places orders when stock is low, VMI shifts the responsibility to the supplier, ensuring a steady flow of critical components. This system enhances efficiency, reduces the burden on procurement teams, and ensures that production lines remain uninterrupted.
The Challenges of Supply Chain Management in Mission-Critical Industries
Industries such as aerospace, military, and medical manufacturing face unique challenges in supply chain management:
Strict Quality and Compliance Requirements: Components must meet rigorous standards to ensure reliability and performance.
Long Lead Times: Many high-reliability electronic components have extended manufacturing cycles, requiring strategic inventory planning.
Obsolescence Risks: Rapid technological advancements can render components obsolete, necessitating proactive inventory strategies.
Unpredictable Demand Fluctuations: Changes in project timelines, government contracts, or unforeseen market demands can disrupt supply chain planning.
How ES Components Enhances VMI Solutions
ES Components provides a structured, proactive approach to Vendor Managed Inventory, ensuring that businesses operating in mission-critical industries can streamline their supply chains with confidence. Here’s how we do it:
1. Data-Driven Inventory Optimization
We utilize advanced data analytics to monitor usage patterns, forecast demand, and optimize stock levels. By analyzing historical trends and real-time data, we ensure that the right components are always available, reducing the risk of stockouts or excess inventory.
2. Customized Inventory Solutions
Every industry has unique needs. ES Components works closely with clients to develop customized VMI programs that align with production schedules, compliance requirements, and risk management strategies. Whether it's buffer stock for high-priority components or just-in-time inventory for lean manufacturing, we tailor solutions for maximum efficiency.
3. Strong Supplier Relationships and Sourcing Expertise
With decades of experience in the high-reliability electronics sector, ES Components has built strong relationships with key suppliers. Our expertise in sourcing ensures a steady supply of components, even when facing global shortages or supply chain disruptions.
4. Reduction in Lead Times and Cost Savings
By managing inventory strategically, we help businesses reduce long lead times and lower procurement costs. Our VMI solutions minimize administrative overhead, reduce emergency orders, and eliminate excess inventory carrying costs, resulting in significant savings.
5. Compliance and Quality Assurance
In industries where component failure is not an option, quality assurance is paramount. ES Components ensures that every part supplied through VMI meets stringent industry standards, including MIL-SPEC, medical-grade, and aerospace certifications.
The Business Impact of ES Components’ VMI Program
Organizations that implement ES Components’ VMI solutions experience tangible benefits, including:
Improved Production Continuity: Eliminating stockouts ensures smooth manufacturing operations.
Lower Procurement Workload: Automating inventory replenishment reduces administrative burdens.
Better Cash Flow Management: Optimized inventory levels free up capital for other strategic investments.
Stronger Supplier Collaboration: A VMI partnership fosters transparency and efficiency across the supply chain.
Conclusion
For companies operating in aerospace, military, medical, and industrial markets, effective inventory management is essential. ES Components’ Vendor Managed Inventory (VMI) solutions provide a streamlined, cost-effective approach to maintaining critical component availability. With a focus on data-driven inventory planning, customized solutions, and a deep understanding of mission-critical supply chain demands, we empower businesses to operate with confidence and efficiency.
Partner with ES Components today to optimize your supply chain and ensure you always have the right components, precisely when you need them.
Hi-Rel Microelectronic Solutions – Where Performance and Durability Are Non-Negotiable
In mission-critical industries like aerospace, defense, and automotive, there is no room for failure. Extreme environments, high radiation exposure, and rigorous operational demands require components that go beyond standard performance—delivering unwavering reliability under the harshest conditions.
In mission-critical industries like aerospace, defense, and automotive, there is no room for failure. Extreme environments, high radiation exposure, and rigorous operational demands require components that go beyond standard performance—delivering unwavering reliability under the harshest conditions.
At ES Components, we specialize in high-reliability (Hi-Rel) microelectronic components engineered for long-term durability, precision, and compliance with the most demanding industry standards. Our advanced solutions ensure consistent performance in space, military, and high-stakes industrial applications, where failure is simply not an option.
With decades of expertise, ES Components offers not only industry-leading semiconductors and electronic components, but also tailored, innovative solutions to meet specific mission requirements. Our portfolio includes radiation-hardened, high-power, and custom-packaged solutions designed to extend operational life and enhance system integrity.
Our Hi-Rel Product Offerings:
Radiation-Hardened MOSFETs & Bipolar Transistors
JANKC die for extreme reliability and enhanced radiation hardness in aerospace & defense applications
High-dose (1Mrad) and low-dose (300Krad) options
LEO and Non-Rad Hard equivalents for cost-sensitive applications
MIL-PRF-123 Certified Capacitors
Equivalent PME MLCCs ranging from 0402 to 2225 sizes
Voltage ratings from 6.3V to 500V
Proven 4,000-hour life test performance
High-Power RF & Thin-Film Substrates
Precision-engineered materials: Alumina, SiO₂, BeO, AlN
Solid gold via processes and high-conductivity traces
Ideal for high-power RF applications
Custom Hi-Rel Packaging Solutions
Turnkey hermetic packaging for single or multiple chips
Supports MIL-PRF-19500, 38534, and 38535 requirements
Solutions for both current and obsolete die
At ES Components, we don’t just supply microelectronics—we engineer reliability into every component. Whether it's a satellite in orbit, a defense system in operation, or an advanced automotive application, trust ES Components to deliver the performance that matters when failure is not an option.
Explore our Hi-Rel solutions today and experience uncompromising quality built for the most demanding environments.
"Ensuring Reliability: The Critical Role of Lot Traceability in Electronic Components"
In today’s high-stakes industries, where precision and reliability are non-negotiable, lot traceability is more than just a best practice—it’s a necessity. At ES Components, we understand that our customers in aerospace, military, medical, and industrial markets rely on high-quality electronic components that meet strict regulatory and performance standards. Lot traceability plays a crucial role in ensuring compliance, counterfeit prevention, and risk mitigation. Here’s why it matters to you.
In today’s high-stakes industries, where precision and reliability are non-negotiable, lot traceability is more than just a best practice—it’s a necessity. At ES Components, we understand that our customers in aerospace, military, medical, and industrial markets rely on high-quality electronic components that meet strict regulatory and performance standards. Lot traceability plays a crucial role in ensuring compliance, counterfeit prevention, and risk mitigation. Here’s why it matters to you.
The Importance of Lot Traceability in Electronic Components
1. Compliance with Industry Regulations
Industries such as aerospace, defense, and medical are subject to strict regulatory requirements, including AS9100, MIL-STD, ISO 13485, and FDA regulations. These standards mandate full traceability of components to verify authenticity, quality, and proper manufacturing processes. Lot traceability helps ensure compliance with these regulations, reducing the risk of using unauthorized or substandard components.
2. Counterfeit Prevention & Supply Chain Security
The global semiconductor supply chain has been increasingly vulnerable to counterfeit parts. A single faulty or fraudulent component can compromise an entire system, leading to severe consequences in mission-critical applications. Lot traceability helps prevent this by allowing customers to verify the origin of components, ensuring they come from authorized manufacturers and distributors. This is particularly critical for military and aerospace applications, where security and reliability are paramount.
3. Failure Analysis & Root Cause Investigation
When a component failure occurs, identifying the root cause quickly is essential to avoid costly downtime and safety risks. Lot traceability allows engineers to trace faulty components back to their manufacturing lot, helping determine whether an issue is isolated or systemic. This is especially important for industries like medical devices and industrial automation, where failures can have life-threatening or costly consequences.
4. Risk Mitigation & Recalls
In the event of a manufacturing defect or quality issue, lot traceability enables targeted recalls, reducing the impact on production and minimizing costs. Without traceability, an entire batch of components—or even an entire product line—may need to be scrapped, leading to unnecessary waste and expenses. With lot tracking, manufacturers can isolate affected parts and take corrective action with precision.
5. Ensuring Consistency & Quality Assurance
For high-reliability applications, consistency across production runs is critical. Lot traceability helps ensure that components used in a system come from the same verified source, maintaining uniform performance, durability, and reliability. This is particularly valuable for aerospace and military customers, where even minor deviations in component performance can lead to catastrophic failures.
6. Geopolitical & Supply Chain Compliance
Governments around the world are tightening supply chain regulations to ensure national security and economic stability. Compliance with acts such as the U.S. NDAA (National Defense Authorization Act) and ITAR (International Traffic in Arms Regulations) requires traceability to ensure components are sourced from approved and trusted suppliers. Lot traceability helps ES Components customers meet these legal requirements, reducing risks associated with unauthorized or restricted sources.
How ES Components Ensures Lot Traceability
At ES Components, we are committed to providing our customers with high-reliability electronic components that meet the most stringent quality standards. Our lot traceability system enables customers to:
Track components from manufacturing to final assembly
Verify authenticity and sourcing from authorized suppliers
Reduce risks of counterfeit or substandard parts
Ensure compliance with industry regulations and government policies
By prioritizing traceability, we empower our customers to operate with confidence, knowing they have complete visibility into their electronic component supply chain.
Conclusion
At ES Components, traceability isn’t just a requirement—it’s our commitment to excellence. We meticulously track every component to guarantee unmatched quality and reliability, giving you the confidence you need in your critical applications. Partner with us today and experience the power of precision, security, and trust in every component we deliver.
Why Engineers Should Consider Using Vishay Intertechnology MLCC Capacitors
Vishay Intertecnology Multi-Layered Ceramic Capacitors manufactured using a cost-efficient base metal electrode (BME) system and dry sheet technology provide an affordable solution for various high-voltage applications.
Manufactured using a cost-efficient base metal electrode (BME) system and dry sheet technology, these MLCCs provide an affordable solution for various high-voltage applications.
Vishay Intertechnology Expands High Voltage MLCC Offerings with Increased Capacitance for Commercial Applications
Vishay Intertechnology, Inc. has introduced a new series of surface-mount multilayer ceramic chip capacitors (MLCCs) designed for high-voltage commercial applications. Available in seven compact case sizes ranging from 1206 to 2225, the VJ….W1HV High Voltage MLCC Commercial Series enhances Vishay’s existing lineup by offering extended capacitance options. These capacitors utilize the ultra-stable C0G (NP0) dielectric and are also available with the X7R dielectric for even greater capacitance levels.
Manufactured using a cost-efficient base metal electrode (BME) system and dry sheet technology, these MLCCs provide an affordable solution for various high-voltage applications. They are ideal for input and output filtering, as well as snubber capacitors in sectors such as renewable and conventional energy systems, power distribution, industrial automation, motor drives, power tools, welding equipment, telecom infrastructure, consumer appliances, and medical instrumentation.
Key specifications include:
C0G (NP0) versions: Voltage ratings up to 3000 VDC, capacitance values ranging from 1.5 pF to 82 nF, and a temperature coefficient of capacitance (TCC) of 0 ppm/°C ±30 ppm/°C from -55 °C to +125 °C.
X7R versions: Capacitance ranging from 100 pF to 100 nF, voltage ratings up to 2000 VDC, and a TCC of ±15% over the same temperature range.
Reliable construction: Featuring nickel barrier with 100% tin terminations, these capacitors are also available with polymer terminations to prevent damage from board flexure.
Additionally, the VJ….W1HV series meets environmental standards by being RoHS-compliant, halogen-free, and Vishay Green.
Why Engineers Should Consider These MLCCs
Extended Capacitance for High-Voltage Applications
Engineers working on power electronics, renewable energy systems, and industrial automation can benefit from the increased capacitance range and high-voltage ratings, making these capacitors suitable for demanding applications.
Reliable Performance in Extreme Conditions
The ultra-stable C0G dielectric ensures minimal capacitance drift over a wide temperature range, while the X7R dielectric offers higher capacitance for designs requiring more energy storage.
Cost-Effective Solution
With a BME system and dry sheet technology, these capacitors offer an affordable alternative without compromising on quality, making them a practical choice for large-scale production.
Enhanced Durability and Board Protection
Engineers designing circuits with potential mechanical stress can opt for polymer terminations, reducing the risk of cracks and failures due to board flexure.
Eco-Friendly and Industry-Compliant
Being RoHS-compliant and Vishay Green, these MLCCs align with modern environmental and safety standards, ensuring sustainable product development.
Conclusion
These features make the VJ….W1HV High Voltage MLCC Series a strong candidate for engineers seeking a high-performance, cost-effective, and durable capacitor solution for their next-generation designs. Discover the collection of MLCC capacitors from Vishay Intertechnology.
Let us help you find the perfect capacitor to elevate your applications and ensure optimal performance.
Avoid These Common Capacitor Failures
Capacitors are crucial in circuit design, yet they’re often overlooked—until they fail. As key components in power, RF, digital, and analog circuits, capacitors are frequently exposed to voltage surges, transients, and harsh environmental conditions. Neglecting their selection and protection can lead to early failures, sometimes catastrophic ones.
Capacitors are crucial in circuit design, yet they’re often overlooked—until they fail. As key components in power, RF, digital, and analog circuits, capacitors are frequently exposed to voltage surges, transients, and harsh environmental conditions. Neglecting their selection and protection can lead to early failures, sometimes catastrophic ones.
Why Capacitors Fail
Capacitors serve critical functions, from filtering noise to voltage regulation. However, they are vulnerable to:
Overvoltage & Transients: Surges, especially in industrial, military, and aerospace applications, can exceed a capacitor’s limits.
Temperature Extremes: Heat and cold affect dielectric integrity, accelerating degradation.
Wear & Tear: Over time, capacitors can leak, corrode, or even explode due to internal pressure buildup.
Mechanical Stress: Shock and vibration may damage delicate internal structures, particularly in through-hole capacitors.
Designing for Reliability
To extend capacitor lifespan and prevent failure:
Choose Higher Ratings: Select capacitors with voltage and temperature margins above expected conditions.
Optimize Placement: Keep them away from heat sources or use shielding for thermal protection.
Consider Ruggedized Components: Use capacitors designed for extreme environments or reinforced with vibration-dampening materials.
Ensure Proper Mounting: Utilize 3D space efficiently to accommodate higher-current components.
Conclusion
Capacitors are essential to the functionality of modern electronics, but their performance hinges on making the right choice and ensuring they’re properly protected. By accounting for real-world factors like voltage spikes, heat, and mechanical stress, you can significantly extend the lifespan of your circuits and avoid costly failures down the road.
Serving as the backbone of electronic systems, capacitors are crucial for controlling current flow and shielding sensitive components. Selecting the right capacitor is not just important—it’s vital to the success of any project. Whether you’re an engineer, hobbyist, or tech enthusiast, mastering capacitor selection empowers you to push the boundaries of your designs. Discover our top-tier collection of capacitors from leading manufacturers—Knowles/Novacap, Vishay EFI, Vishay Sprague, and Vishay Vitramon—available exclusively through ES Components. Let us help you find the perfect capacitor to elevate your applications and ensure optimal performance.
The Engineer’s Guide to Selecting the Perfect Resistor
Resistors are essential components in electronic circuits, regulating current flow and ensuring stable operation. While there are various types, thick film and thin film resistors are among the most widely used—especially in industries like aerospace, military, medical, and industrial applications. But what sets them apart? Let’s break it down.
Resistors are the backbone of electronic circuits, controlling current flow, defining voltage levels, and protecting sensitive components like MOSFETs. Choosing the right resistor is critical for performance, efficiency, and reliability. This guide breaks down resistor types, key specifications, and real-world applications so you can make informed design decisions.
Understanding Resistors: The Fundamentals
A resistor is a passive electrical component that limits current flow, causing a voltage drop across its terminals. The three primary characteristics engineers consider when selecting a resistor are:
Resistance (Ω): The opposition to current flow, determining how much voltage drops across the resistor.
Power Rating (W): The maximum power a resistor can dissipate before overheating. Common values range from 1/8 W to 1 W for standard applications, but higher power resistors are available.
Tolerance (%): The precision of the resistor's stated resistance, typically ±1%, ±5%, or ±10%.
Types of Resistors and Their Ideal Uses
Different resistor types serve different engineering needs. Here’s a breakdown of the most common ones:
1. Carbon Film Resistors
Description: Composed of a thin carbon layer over a ceramic core.
Best For: General-purpose applications in consumer electronics and audio equipment.
Advantages: Cost-effective, widely available, and sufficient for non-precision circuits.
2. Metal Film Resistors
Description: A thin metal layer provides greater precision and stability.
Best For: High-frequency circuits and precision applications.
Advantages: Low noise, high accuracy (±1% tolerance), and excellent stability over time.
3. Wirewound Resistors
Description: A resistive wire (often nichrome) wound around a core.
Best For: High-power and precision applications.
Advantages: Superior heat dissipation and high power ratings.
4. Ceramic Resistors
Description: High-temperature-resistant ceramic materials.
Best For: High-power applications like power supplies.
Advantages: Excellent thermal stability and rugged durability.
5. Variable Resistors (Potentiometers & Rheostats)
Description: Adjustable resistance for tuning circuit performance.
Best For: Volume controls, adjustable power supplies, and sensor calibration.
Advantages: Versatile, allowing real-time adjustments.
6. Surface Mount Resistors (SMD)
Description: Compact resistors designed for automated assembly on PCBs.
Best For: Modern miniaturized electronics and high-density PCB designs.
Advantages: Space-efficient and optimized for high-speed manufacturing.
Practical Engineering Applications of Resistors
Resistors play a critical role in countless circuit functions. Here’s how engineers implement them:
1. Voltage Division
Used to create reference voltages via a voltage divider circuit.
Exploits Kirchhoff’s Voltage Law to distribute voltage proportionally.
2. Current Limiting
Protects sensitive components from excessive current.
Example: A 440 Ω resistor in series with an LED ensures safe operation and longevity.
3. Pull-Up and Pull-Down Resistors
Ensures stable logic levels in digital circuits.
Essential for microcontrollers and logic gates where floating inputs can cause erratic behavior.
4. Transistor Biasing
Determines the operating point of a transistor in amplifier circuits.
Ensures consistent and predictable transistor performance.
5. Signal Filtering
Combined with capacitors to form low-pass, high-pass, and band-pass filters.
Shapes signal frequencies for applications like audio processing and RF circuits.
Conclusion
Resistors are the most fundamental components in the world of electronics. Resistors are essential for controlling the flow of current and protecting sensitive electronic components. Understanding how to use the right resistor is crucial for any and every electronics project. Whether you're an engineer, hobbyist, or tech enthusiast, a deeper understanding of these components empowers you to innovate and optimize your designs. Explore our selection of high-quality resistors from world-class manufacturer—Vishay Intertechnology,—proudly offered through ES Components. Let us help you find the perfect solution for your applications
Revolutionizing Power Electronics with Microchip’s mSiC™ Technology
In today’s high-performance industries, efficiency, reliability, and power density are critical. Whether designing cutting-edge electric vehicles, aerospace systems, industrial equipment, or medical devices, engineers are constantly searching for solutions that push the boundaries of innovation.
In today’s high-performance industries, efficiency, reliability, and power density are critical. Whether designing cutting-edge electric vehicles, aerospace systems, industrial equipment, or medical devices, engineers are constantly searching for solutions that push the boundaries of innovation.
Enter Microchip’s Silicon Carbide (SiC) technology…a game-changer in power electronics. Engineered for demanding applications, SiC MOSFETs and Schottky Barrier Diodes (SBDs) offer a superior alternative to traditional silicon-based components, providing higher efficiency, lower losses, and unmatched durability.
Why Choose Microchip SiC?
Microchip’s SiC solutions provide industry-leading advantages that set them apart:
✅ Unmatched Efficiency for Maximum Performance
Traditional silicon-based power devices suffer from significant switching and conduction losses, reducing overall system efficiency. Microchip’s SiC MOSFETs and SBDs are designed with ultra-low switching losses, minimizing energy waste and maximizing output—an essential factor for high-power applications.
✅ Compact, Lightweight Designs
Size and weight are critical factors in industries like automotive, aerospace, and medical. With higher power density and reduced cooling requirements, Microchip SiC devices enable smaller, more lightweight power systems—making them ideal for compact designs that demand superior power handling.
✅ Superior Thermal Conductivity for Better Heat Dissipation
Heat management is a major challenge in high-power applications. Silicon Carbide boasts 3× better thermal conductivity than silicon, allowing for improved heat dissipation and reducing the need for bulky heat sinks and cooling systems. The result? Cooler, more efficient operation and longer component lifespan.
✅ Rugged and Reliable for Extreme Environments
Microchip’s SiC technology is designed to thrive under harsh conditions, making it the perfect choice for applications that demand high reliability. With the ability to operate at higher temperatures without degradation, these components ensure long-term durability in even the most challenging environments—from the battlefield to industrial automation systems.
✅ AEC-Q101 Qualified – Meeting Industry Standards
Reliability isn’t just a claim—it’s a guarantee. Microchip’s SiC MOSFETs and SBDs meet AEC-Q101 qualification standards, ensuring they are rigorously tested and proven for automotive and industrial applications. When you choose Microchip, you choose a product that meets the strictest quality benchmarks.
Applications: Powering the Future Across Industries
Microchip’s SiC technology is revolutionizing industries that demand high efficiency, reliability, and performance:
🚗 Automotive – Electric vehicles (EVs), charging infrastructure, and powertrain systems
🏭 Industrial – High-power motor drives, renewable energy systems, and grid infrastructure
🛩️ Aerospace & Defense – Avionics, radar systems, and military-grade power electronics
🏥 Medical – Advanced medical imaging, surgical equipment, and high-precision instruments
Whether designing for automotive electrification, energy-efficient industrial systems, or mission-critical aerospace applications, Microchip SiC is the power solution for the future.
Ready to Upgrade? ES Components Has Microchip SiC In Stock!
At ES Components, we understand that quality, availability, and support are just as important as performance. That’s why we proudly stock Microchip SiC Bare Die, ready to ship when you need them.
🔹 Reliable Supply Chain – Avoid long lead times with our ready-to-ship inventory
🔹 Made in the USA – Ensuring top-tier quality and compliance with industry standards
🔹 Trusted Partner – Supporting aerospace, military, medical, and industrial markets
Unlock the Full Potential of SiC with Microchip and ES Components
As industries move toward higher efficiency and smarter power solutions, Silicon Carbide is leading the charge. Don’t settle for outdated silicon-based components—upgrade to Microchip SiC today and experience unmatched power, efficiency, and reliability.
📦 Contact ES Components now to secure your Microchip SiC components!
Exploring the Different Types of Diodes and Their Unique Function
Diodes are essential components in modern electronics, playing a crucial role in various applications across industries. These tiny yet powerful devices regulate current flow, ensuring efficiency and functionality in circuits. Below, we explore some of the most widely used types of diodes and their unique characteristics.
Diodes are essential components in modern electronics, playing a crucial role in various applications across industries. These tiny yet powerful devices regulate current flow, ensuring efficiency and functionality in circuits. Below, we explore some of the most widely used types of diodes and their unique characteristics.
1. Standard Diode
A diode is a two-terminal electronic component that acts as a one-way valve for electrical current. It allows current to flow easily in one direction while blocking it in the other, making it fundamental in rectifiers and power conversion applications.
2. Light-Emitting Diode (LED)
The LED is more than just a light source—it revolutionized illumination technology! When voltage is applied, electrons recombine with holes in the semiconductor, releasing energy as photons. This process, known as electroluminescence, is responsible for the vibrant colors and energy efficiency of LED lighting used in homes, cars, and digital displays.
3. Photodiode
Designed to convert light into electrical current, the photodiode is an essential component in light detection applications such as cameras, solar panels, and optical communication systems. It generates an electrical response when exposed to light, making it a key player in renewable energy and sensor technology.
4. Schottky Diode
Named after physicist Walter H. Schottky, the Schottky diode is known for its low forward voltage drop and ultra-fast switching speed. This makes it ideal for high-frequency applications, including power regulation, radio frequency (RF) circuits, and voltage clamping.
5. Transient Voltage Suppression (TVS) Diode
The TVS diode acts as a guardian against voltage spikes, protecting sensitive electronics from sudden power surges. It is commonly used in circuit protection for devices like microcontrollers, automotive electronics, and telecommunications equipment.
6. Tunnel Diode
The tunnel diode, also known as the Esaki diode, leverages quantum mechanics to enable extremely fast operation—even in the microwave frequency range! This makes it a valuable component in high-speed electronics and RF applications.
7. Varicap (Varactor) Diode
The varicap diode, also called a varactor diode, is unique in that its capacitance changes with applied voltage. This feature allows it to be used in frequency tuning applications, such as radio tuners, phase-locked loops, and voltage-controlled oscillators.
8. Zener Diode
Unlike conventional diodes, the Zener diode not only allows current to flow forward but also in reverse when a specific voltage—called the Zener voltage—is reached. This makes it indispensable in voltage regulation, surge protection, and power supply stabilization.
Conclusion
From illuminating our world with LEDs to stabilizing voltage with Zener diodes, each type of diode plays a crucial role in modern electronics. Whether you're an engineer, hobbyist, or tech enthusiast, a deeper understanding of these components empowers you to innovate and optimize your designs.
Explore our selection of high-quality diodes from world-class manufacturers—Vishay Intertechnology, VPT Components, and Microchip Technology—proudly offered through ES Components. Let us help you find the perfect solution for your applications.