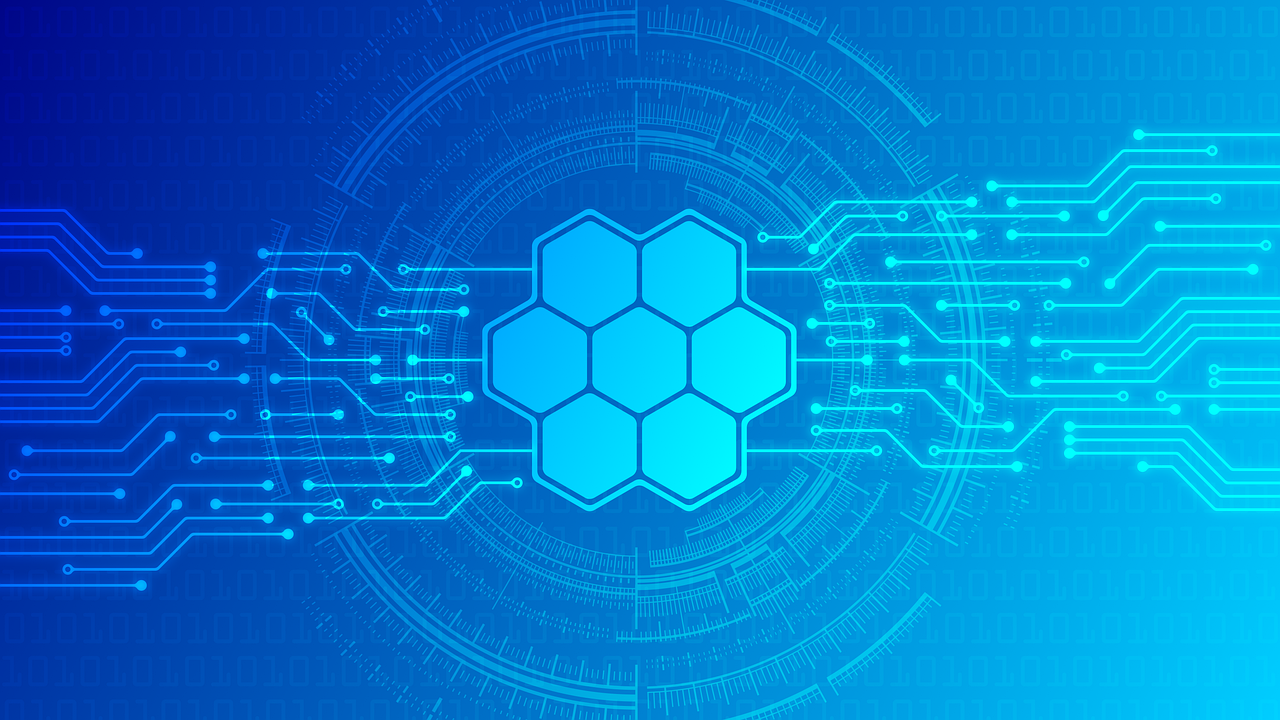
TECH TALK
High Reliability Insights From ES Components
The Official Blog of
Buy Bare Die Like a Pro: Insider Secrets Revealed
Navigating the world of Bare Die can be overwhelming if you're new to it. Unlike standard packaged semiconductors, purchasing bare die isn’t as simple as searching for a part number online. Many suppliers view it as a niche market, making it even trickier to source. However, once you understand the key differences between packaged components and bare die, you’ll be well on your way to buying like a seasoned expert.
Navigating the world of Bare Die can be overwhelming if you're new to it. Unlike standard packaged semiconductors, purchasing bare die isn’t as simple as searching for a part number online. Many suppliers view it as a niche market, making it even trickier to source. However, once you understand the key differences between packaged components and bare die, you’ll be well on your way to buying like a seasoned expert.
Step 1: Find a Trusted Bare Die Supplier
The first and most critical step is to partner with a reputable bare die supplier. A knowledgeable supplier can guide you through the complexities of the process, ensuring you get the right components with the necessary:
Certificates of Conformance
Lot Traceability
Source Control Drawings
Geometries and Specific Testing Requirements
Since not all bare die components are readily available, working with an experienced supplier will save you time, reduce risk, and prevent costly mistakes.
Step 2: Understand the Manufacturing Process
Manufacturers produce bare die by fabricating wafers, which are then tested and cut into individual die. These die are assigned part numbers before being shipped to specialized bare die distributors.
At this stage, distributors conduct Lot Acceptance Testing (LAT) to verify the quality of the die. Additional testing methods, such as Known Good Die (KGD) verification, further ensure reliability.
Step 3: Know What to Expect from Distributors
When purchasing bare die, visual inspection is critical. Experienced distributors apply military-grade inspection techniques to identify flawless die that are likely to function optimally.
However, several factors can impact availability:
Some parts may not be available in bare die form.
Minimum purchase quantities from manufacturers may exceed your needs.
Die geometries change over time, so keeping updated specifications is essential.
Working with a trusted supplier ensures you receive accurate information and, when necessary, sample die for qualification and testing.
The Industries That Rely on Bare Die
Bare die technology is the go-to solution for applications where size, performance, and reliability are paramount. Industries such as:
✔ Aerospace
✔ Military & Defense
✔ Avionics
✔ Medical Implants
✔ Automotive
✔ High-End Industrial Applications
… all depend on bare die for their cutting-edge designs.
Final Takeaway
Buying bare die doesn’t have to be intimidating. By partnering with a trusted supplier, understanding the manufacturing process, and knowing how distributors operate, you’ll be well-equipped to buy bare die like a pro.
Thick vs. Thin Film Resistors: Understanding the Differences
Resistors are essential components in electronic circuits, regulating current flow and ensuring stable operation. While there are various types, thick film and thin film resistors are among the most widely used—especially in industries like aerospace, military, medical, and industrial applications. But what sets them apart? Let’s break it down.
Resistors are essential components in electronic circuits, regulating current flow and ensuring stable operation. While there are various types, thick film and thin film resistors are among the most widely used—especially in industries like aerospace, military, medical, and industrial applications. But what sets them apart? Let’s break it down.
The Core Difference: Manufacturing Process
The primary distinction between thick and thin film resistors lies in how the resistive material is applied:
Thin Film Resistors: Manufactured through a process called sputtering, a vacuum deposition method that allows precise control over the film thickness. The material—often a ceramic-metal (cermet) compound like tantalum nitride (TaN) or nickel-chromium (NiCr)—is etched using a photolithographic process, similar to how printed circuit boards (PCBs) were traditionally made.
Thick Film Resistors: Created through screen and stencil printing, where conductive materials (like ruthenium oxide or bismuth iridate) are mixed with a carrier liquid and applied to a ceramic base. The composite is then baked at around 850°C to form the final resistor.
Performance Comparison
Accuracy & Stability
Thin film resistors offer greater precision, with typical tolerances of 1% or even 0.5%, while thick film resistors have improved over time, now offering 1% or 2% tolerances as standard. Thin film resistors also have lower temperature coefficients, ranging from 5 to 50 ppm/K, whereas thick film resistors typically range between ±200 to ±250 ppm/K—meaning resistance can fluctuate more with temperature changes.
Noise Levels
For applications requiring low noise, thin film resistors are the preferred choice. They generate 10 to 100 times less noise than thick film resistors, making them ideal for precision analog circuits.
Cost Consideration
Thin film resistors, with their higher precision and stability, come at a price. In bulk, they can cost twice as much as thick film resistors of similar specifications. This cost difference often determines which type is used, with thick film resistors being more common in cost-sensitive applications.
Which One Should You Choose?
Use Thin Film Resistors When:
Precision and stability are critical (e.g., medical devices, aerospace, military applications).
Low noise and tight tolerances are required.
The budget allows for higher component costs.
Use Thick Film Resistors When:
Cost efficiency is a priority.
High precision is not necessary.
The circuit can tolerate higher temperature variations.
Final Thoughts
Both thick and thin film resistors have their place in modern electronics. Whether you're designing circuits for consumer electronics or high-reliability aerospace systems, understanding the differences will help you make the right choice for your application. View Vishay EFI Thin Film Resistors to see if this is a solution for you.
Would you like assistance selecting the best resistor for your project? Contact ES Components today for expert guidance!
Accelerate Your Innovation: The Future of Value-Added Solutions
In today’s fast-paced world, getting your innovations to market quickly is the key to staying ahead. But what if you had a partner that didn’t just supply components—but enhanced your entire process?
In today’s fast-paced world, getting your innovations to market quickly is the key to staying ahead. But what if you had a partner that didn’t just supply components—but enhanced your entire process?
At ES Components, we go beyond traditional distribution. Our value-added solutions are designed to optimize productivity, improve efficiency, and ensure you get exactly what you need, precisely when you need it. By prioritizing quality, customization, and attention to detail, we provide a seamless, tailored experience that helps you bring your vision to life—faster and more efficiently.
When every second counts, trust a partner who understands that the details make the difference. Experience the future of value-added solutions—because innovation shouldn’t wait.
Why Engineers Should Rely on Distributors for Component Sourcing
As an engineer, your job is to bring a concept to life. Whether you're designing a custom power supply or assembling a complex electronic system, one thing is certain—you need parts. Lots of them. But where should you source them? Should you spend hours navigating multiple manufacturer websites, or is there a better way?
As an engineer, your job is to bring a concept to life. Whether you're designing a custom power supply or assembling a complex electronic system, one thing is certain—you need parts. Lots of them. But where should you source them? Should you spend hours navigating multiple manufacturer websites, or is there a better way?
The answer is clear: partnering with a distributor simplifies and streamlines the process, making your job easier and your projects more efficient. Here’s why choosing a distributor is the smart move for engineers dealing with extensive bills of materials (BOMs):
1. One-Stop Shopping for Every Component
Think of sourcing components like ordering a meal. You wouldn’t go to separate restaurants for your burger, fries, and drink—it’s far more convenient to get everything from one place. The same applies to electronics. Distributors stock millions of parts from multiple manufacturers, giving you a single source for everything you need.
2. Efficient BOM Management
A distributor's platform provides powerful BOM tools that streamline the entire process. These tools help verify part availability, suggest alternatives, and ensure order accuracy. Instead of spending hours cross-referencing part numbers, you can make informed decisions quickly.
3. Access to Comprehensive Online Resources
Need technical specs? No problem. Distributors offer detailed datasheets, product descriptions, specifications, and application notes. Many also provide BOM management tools, conversion calculators, and search accelerator plug-ins—helping you design smarter and faster.
4. Collaborative Project & Cart Sharing
Working in a team? Many distributors allow engineers to share their projects and shopping carts with colleagues or procurement teams. This feature helps ensure that the right parts are being ordered and that everyone stays on the same page.
5. Flexible Order Quantities & Fast Shipping
Whether you need a single prototype component or a bulk order of thousands, distributors offer flexible purchasing options. Plus, with centralized sourcing, you can consolidate shipping and receive all your parts in one delivery—often with same-day processing.
6. Superior Customer Support & Technical Assistance
Forget navigating multiple customer service lines. Distributors provide dedicated technical support, online chat, and order tracking. You also gain access to historical purchase records, making reordering seamless.
7. Simplified Logistics & Cost Savings
Ordering from multiple manufacturers means juggling different shipping schedules, payment processes, and tracking numbers—not to mention paying for separate shipping fees. A distributor consolidates everything, saving you time, hassle, and money.
The Bottom Line
Time is a valuable resource, and efficiency is key in engineering. Using a distributor eliminates unnecessary complications, allowing you to focus on what really matters—bringing your project to life. So next time you're sourcing components, make the smart choice. Choose a distributor and streamline your entire process.
"Active & Passive Components - What Is The Difference Between The Two?
Active Components are made up of Diodes, Integrated Circuits, MOSFETs, JFETs, Optoelectronics, Oscillators and Transistors. Passive Components are made up of Capacitors, Inductors/Magnetics, Resistors, Substrates & Interconnects, Energy and High Frequency Components.
ACTIVE COMPONENTS are made up of Diodes, Integrated Circuits, MOSFETs, JFETs, Optoelectronics, Oscillators and Transistors. PASSIVE COMPONENTS are made up of Capacitors, Inductors/Magnetics, Resistors, Substrates & Interconnects, Energy and High Frequency Components.
Passive Electronic Components
Active Electronic Components
SEMICONDUCTORS |
TRANSISTORS |
|
|
BASIC COMPONENTS |
ELECTROMECHANICAL COMPONENTS |
|
|
What’s The Difference?
Active Components |
Passive Components |
Active Device transforms and injects power or energy into a circuit. |
Passive Device utilizes power or energy into a circuit. |
Examples: Diode, Transistor, SCR, ICs, DC generator, Current & Voltage sources etc. |
Examples: Resistors, Capacitors, Inductors, Transformer, Motors etc. |
Active element produces energy in the form of voltage or current |
Passive element stores energy in the form of voltage or current. |
They have function and provide power gain (Amplifier). |
They do not have function provide power gain. |
It can control the flow of current. |
It cannot control the flow of the current. |
Active components require an external & conditional source to operate in the circuit. |
Passive Components do not require any external source to operate in the circuit. |
They have gain more than 1, so they can amplify the signal. |
They have gain less than 1, so they can’t amplify the signal. |
They are energy donor. |
They are energy acceptor |
They lay in Linear category |
They lay in Non-Linear category. |
The Two Types of Electronic Devices
Electronic elements that make up a circuit are connected together by conductors to form a complete circuit.
Active components
Passive components
Active Components
An active component is an electronic component which supplies energy to a circuit.
Common examples of active components include:
Voltage sources
Current sources
Generators (such as alternators and DC generators)
All different types of transistors (such as bipolar junction transistors, MOSFETS, FETs, and JFET)
Diodes (such as Zener diodes, photodiodes, Schottky diodes, and LEDs)
Voltage Sources
A voltage source is an example of an active component in a circuit. When current leaves from the positive terminal of the voltage source, energy is being supplied to the circuit. As per the definition of an active element, a battery can also be considered as an active element, as it continuously delivers energy to the circuit during discharging.
Current Sources
A current source is also considered an active component. The current supplied to the circuit by an ideal current source is independent of circuit voltage. As a current source is controlling the flow of charge in a circuit, it is classified as an active element.
Transistors
Although not as obvious as a current or voltage source – transistors are also an active circuit component. This is because transistors are able to amplify the power of a signal (see our article on transisors as an amplifier if you want to know exactly how).
Passive Components
A passive component is an electronic component which can only receive energy, which it can either dissipate, absorb or store it in an electric field or a magnetic field. Passive elements do not need any form of electrical power to operate.
As the name ‘passive’ suggests – passive devices do not provide gain or amplification. Passive components cannot amplify, oscillate, or generate an electrical signal.
Common examples of passive components include:
Resistors
Inductors
Capacitors
Transformers
Resistors
A resistor is taken as a passive element since it can not deliver any energy to a circuit. Instead resistors can only receive energy which they can dissipate as heat as long as current flows through it.
Inductors
An inductor is also considered as passive element of circuit, because it can store energy in it as a magnetic field, and can deliver that energy to the circuit, but not in continuous basis. The energy absorbing and delivering capacity of an inductor is limited and transient in nature. That is why an inductor is taken as a passive element of a circuit.
Capacitors
A capacitor is considered as a passive element because it can store energy in it as electricfield. The energy dealing capacity of a capacitor is limited and transient – it is not actually supplying energy, it is storing it for later use.
As such it is not considered an active component since no energy is being supplied or amplified.
Transformers
A transformer is also a passive electronic component. Although this can seem surprising since transformers are often used to raise voltage levels – remember that power is kept constant.
When transformers step up (or step down) voltage, power and energy remain the same on the primary and secondary side. As energy is not actually being amplified – a transformer is classified as a passive element.
Source: Electrical 4U.com
"Silicon Carbide: Advancing Power Electronics for the Future"
Explore the fundamentals and history of Silicon Carbide (SiC) technology. Build a strong foundation and deepen your expertise in advanced semiconductors.
Explore the fundamentals and history of Silicon Carbide (SiC) technology. Build a strong foundation and deepen your expertise in advanced semiconductors.
Transforming Power Electronics with Silicon Carbide
In the rapidly evolving field of power electronics, Silicon Carbide (SiC) is transforming the way industries operate, offering higher efficiency, durability, and performance compared to traditional silicon-based semiconductors. From electric vehicles (EVs) and aerospace to renewable energy systems and industrial automation, SiC’s exceptional properties—such as its ability to withstand high temperatures, voltages, and frequencies—are paving the way for next-generation technological advancements.
Why Silicon Carbide? The Science Behind the Breakthrough
Silicon Carbide’s superiority stems from its fundamental material properties, making it the preferred choice for high-performance power electronics. Here’s what sets SiC apart:
Wide Bandgap – With a bandgap nearly three times that of silicon, SiC allows for higher electric field strength, enabling power devices to operate at greater efficiencies and voltages.
High Thermal Conductivity – SiC dissipates heat much faster than silicon, allowing devices to operate at higher temperatures without degrading performance, making them ideal for compact, high-power applications.
Chemical Inertness – Resistant to oxidation and chemical corrosion, SiC-based components excel in harsh industrial and aerospace environments.
High Breakdown Voltage – SiC can withstand significantly higher voltages than silicon, enabling the development of thinner, more efficient power electronics with reduced energy losses.
These properties not only enhance performance but also enable smaller, lighter, and more efficient designs, making SiC crucial for high-power applications.
A Brief History: From Stardust to Semiconductors
The story of Silicon Carbide dates back over a century, with its first synthetic production in the late 1800s. However, naturally occurring SiC, known as moissanite, was initially discovered in meteorites, showcasing its extraterrestrial origins. On Earth, SiC was historically used as an abrasive material due to its hardness but later emerged as a promising semiconductor material with revolutionary potential.
Advancements in manufacturing techniques, such as the Lely method and chemical vapor deposition (CVD), have enabled the production of high-purity SiC wafers, which are now widely used in power electronics. This progress has allowed SiC to transition from a niche material to a dominant force in next-generation semiconductor technology.
The Growing Impact of SiC in Power Electronics
Electric Vehicles (EVs) and Transportation
SiC power electronics are transforming EV powertrains, inverters, and charging systems. With SiC-based components, EVs can achieve:
Higher energy efficiency, leading to extended driving range.
Faster charging times due to improved thermal management.
Reduced weight and size, enhancing overall vehicle performance.
Leading EV manufacturers, including Tesla, Toyota, and BYD, have already integrated SiC technology into their systems, significantly improving vehicle efficiency and battery performance.
Renewable Energy and Smart Grids
SiC’s high efficiency is crucial for solar and wind energy systems, where power conversion and management play a pivotal role. SiC-based inverters and converters help:
Reduce energy losses during power conversion.
Enhance reliability in high-voltage applications.
Improve grid stability, allowing for more efficient power distribution.
Aerospace and Defense
SiC’s ability to withstand extreme conditions makes it ideal for high-performance radar systems, satellite power management, and military applications. The U.S. Department of Defense and NASA are actively researching SiC’s potential for deep-space exploration and advanced weaponry systems.
Industrial Automation and High-Voltage Applications
SiC is reshaping industries that demand high voltage and efficiency, such as factory automation, robotics, and high-speed rail systems. Its superior durability and thermal properties contribute to more reliable and long-lasting systems in harsh industrial environments.
The Future of Silicon Carbide in Power Electronics
As demand for high-efficiency power electronics grows, SiC is poised to play a critical role in next-generation technologies. The material is expected to drive advancements in:
5G and telecommunications, improving energy efficiency and signal integrity.
Next-generation computing, where high-frequency power devices are essential.
Medical equipment, enhancing power management in life-saving devices.
Market analysts predict that the SiC semiconductor market will grow exponentially, with major investments from companies such as Wolfspeed, STMicroelectronics, ON Semiconductor, and Infineon Technologies. Researchers are also exploring gallium nitride (GaN) and SiC hybrid systems, which could further optimize power electronics in the future.
Conclusion
Silicon Carbide is more than just a semiconductor—it’s a catalyst for innovation in power electronics. With its unmatched efficiency, high-temperature tolerance, and superior voltage-handling capabilities, SiC is enabling the next era of electrification, automation, and sustainability.
For engineers, technologists, and innovators, mastering SiC’s fundamentals is essential to unlocking its full potential. As industries continue to push the boundaries of efficiency and performance, SiC is at the forefront of this technological revolution—driving the future of power electronics, one breakthrough at a time.
What Are Electronic Component Packaged Devices or Integrated Circuit Packaging?
In very simple terms, Packaged Devices is nothing more than an encasement that surrounds the circuit device to protect it from physical impairment or corrosion. In addition, it also allows electrical contacts that are mounted on the device to connect to a printed circuit board.
Reference: Wikipedia
In very simple terms, Packaged Devices is nothing more than an encasement that surrounds the circuit device to protect it from physical impairment or corrosion. In addition, it also allows electrical contacts that are mounted on the device to connect to a printed circuit board
Short History: Early 1970’s through early 2000’s.
So how did all this stuff start with Packaged Devices? The earliest integrated circuits were packaged in what are called “Ceramic Flat Packs”. These were a
Military standardized printed circuit board surface mount component packages or “Flat Packs” The other type of packaging used in the 1970s, was called the
ICP (Integrated Circuit Package). After that, these “Packaged Devices” kept evolving as technology advanced. Commercial circuit packaging quickly moved to
DIP or Dual-In-Line Packaging made from ceramic and then later plastic.
Next came PGA or Pin-Grid Array and LCC, Leadless Chip Carrier. After that, Surface Mount Packaging appeared to be the next new thing. The electrical components could be mounted directly onto the surface of the printed circuit board. Then came the Small Outline Integrated Circuit that occupied an area about 30-50% less than the Dual In-Line Packaging.
Next was the area array package, that was a ceramic Pin Grid Array Package
Then there was the Ball Grid Array or BGA. but evolved into Flip-Chip Ball Grid Array (FCBGA) packages in the 1990s. FCBGA packages allow for much higher pin count than any existing package types. In an FCBGA package, the die is mounted upside-down (flipped) and connects to the package balls via a substrate that is similar to a printed-circuit board rather than by wires. FCBGA packages allow an array of input-output signals (called Area-I/O) to be distributed over the entire die rather than being confined to the die periphery.
OPERATION PROPERTIES: (DIE)
Traces out of the die, through the package, and into the printed circuit board have very different electrical properties, compared to on-chip signals. They require special design techniques and need much more electric power than signals confined to the chip itself.
Recent developments consist of stacking multiple dies in single package called SiP, for System In Package, or three-dimensional integrated circuit. Combining multiple dies on a small substrate, often ceramic, is called an MCM, or Multi-Chip Module. The boundary between a big MCM and a small printed circuit board is sometimes blurry.
WHAT DOES THIS ALL MEAN TO A “NON-ENGINEER?”
Well, to help you when you are searching for these devices, here are some common Package Types and images of these Packaged Devices.
Are you soldering to the top contact or wire bonding?
This is a must if there are any power discrete devices on the BOM. Many discrete die are available with either option. The rest are only offered with one or the other of these two options. If only solderable top metal is available, and there are no alternative devices, the die distributor can possibly offer a sub-assembly using a Copper or Molybdenum disk with suitable top plating to meet wire bond requirements.
How are you planning to attach the die?
The vast majority of power discretes are available from the manufacturer with solderable back metal only, some with either solderable or gold back metal. If the user is planning to use epoxy attach, it is highly recommended that they not use die with solderable metals. Gold back metal is recommended for either eutectic or epoxy attach. At ES Components we have developed and qualified the ability to remove solderable back metal from wafers and deposit gold for devices where this option is not available from the vendor. Silicon back die are generally epoxy-attached and if a eutectic attach is required, a gold alloy preform is needed.
How will you want this bare die packaged for delivery in full production?
Packaged parts are typically supplied in production quantities on tape-and-reel with nearly infinite shelf life. Waffle packs are the most common medium for shipping bare die, but high volume automatic assemblies are moving towards sawn wafer on film to reduce cost and enhance manufacturing throughput. However, sawn wafer on film has shelf life limitations which demand special management of the supply pipeline. A die distributor can manage the pipeline so that probed unsawn wafers are kept in stock in the appropriate environment and sawn wafers on film are limited to only those wafers needed for short-term production. If there is a delay in manufacturing, the unsawn wafer inventory remains pristine and the shelf life issue is confined to a small subset of the inventory.
Summary
By answering these questions at the time of initial contact and early in the design process, it’s possible to save the user time and money by avoiding the need to modify or redesign the function based on sample evaluation possibly weeks or even months later. We can also properly code the die part number to capture all the pertinent information for future reference.
Optimizing Bare Die Selection for Reliable Hybrid Microcircuits
Unless you have been doing this for a good number of years you will quickly find out that there is a lot more involved than just searching for a Part# on the Internet. It’s especially frustrating to find out that in a world of “packaged” semiconductors that Bare Die commerce is perceived as a bother. The trick is understanding the differences between packaged parts and bare die.
Unless you have been doing this for a good number of years you will quickly find out that there is a lot more involved than just searching for a Part# on the Internet. It’s especially frustrating to find out that in a world of “packaged” semiconductors that Bare Die commerce is perceived as a bother. The trick is understanding the differences between packaged parts and bare die.
What is Bare Die and how do I buy Bare Die?
Manufacturers produce a wafer that yields the die. After testing the wafer, individual die are separated from the wafer and assigned a part number and then shipped to a bare die distributor. Here, samples from a die lot are packaged to expedite Lot Acceptance Testing (LAT). Additional testing is usually done through a method of Known Good Die (KGD).
First, find a trusted Bare Die supplier that can provide you with the components in die form. Their expertise and advice will help you in the buying process. You may need Certificates of Conformance, Lot Traceability, Source Control Drawings, Geometries, Specific Testing performed. It can be very confusing.
Manufacturers produce a wafer that yields the die. After testing the wafer, individual die are separated from the wafer and assigned a part number and then shipped to a bare die distributor. Here, samples from a die lot are packaged to expedite Lot Acceptance Testing (LAT). Additional testing is usually done through a method of Known Good Die (KGD).
At the distributor’s facility, the die is visually reinspected to make sure that the die that you purchase looks flawless and will function well. In some instances, additional electrical testing is also performed for screening of specific electrical parameters. Current die geometries must be obtained and any changes that have occurred must be forwarded to the end customer for review and approval. Often times samples are required by the end customer. Depending on the device, the distributors can usually provide the required sample. Sometimes though, the part is not available from the manufacturer in die form, or if the manufacturer agrees to provide the part, the minimum purchase quantity may be much, much higher than the end customer requires. Always keep in mind that everything is NOT available in die form.
Specifying and obtaining the correct bare die to build hybrid microcircuits and multi-chip modules presents some specific problems. Dominant design factors here are hermetic sealing requirements, size, and weight. However, the special needs related to the supply of bare die continues to mystify much of the electronics community beyond the handful of hybrid manufacturers specifically focused on this market.
Most hybrids are designed around the characterization of packaged parts. Once samples are received, the function designer builds the breadboard, runs characterization data, and then asks the hybrid designers to create a hybrid or multi-chip module to simulate the function. Here is where the die distributor immediately begins to add value.
Taking the Bill Of Materials (BOM) from the customer, we immediately determine which of the requested parts are not readily available in die form or require added value processing. First, some semiconductor devices are not available as bare die because the manufacturer simply elects not to offer the device in die form. Many newer power discrete devices are assembled in packages that use a braised clip for the top contact attachment point. The top metal used to facilitate these packages is not suitable for wire bonding or soldering, so the manufacturer will not offer this die to the market.
In this era of large wafer diameters of 6-in. or 8-in. and larger, the manufacturer may elect not to 100 percent-probe smaller die at the wafer level. The manufacturer does sample probes only, and accepts the predicted yield loss during 100 percent test of the packaged part.
In some cases, parts that have no prior history in the die market may have prohibitively high minimum order requirements in die or wafer form from the manufacturer, making it impossible to sample or support prototype builds.
The die distributor can address each of these problems and either perform the required added value or recommend a list of alternatives that are more readily available. In the case where a manufacturer will simply not quote a bare die, the die distributor often has access to alternative sources that can offer die with similar functions.
Suitability for Wire Bonding
Where the top metal is not suitable for wire bonding, it is usually not difficult to find a similar device within the vendor portfolio that is offered in die form with the preferred metallization. In the case where 100 percent probe is not performed by the manufacturer, the die distributor can offer this service using in-house capabilities or outsourcing to an approved test lab. This also involves the distributor performing a Lot Acceptance Test (LAT) after probe, to provide objective evidence that the probe successfully met the specified requirements.
Stocking and Inventory Control
At ES Components, we have proactively identified a long list of popular devices throughout our line card and established an “off-the-shelf” inventory. This inventory is automatically replenished based on a predetermined min/max rather than market demand. An off-the-shelf part is immediately available for sampling and has virtually no Minimum Order Quantity (MOQ) when supporting prototype procurements. The products offered include a variety of analog micro-circuits and a compete portfolio of popular discrete die and thin film resistor chips. We use this preferred inventory to quickly offer the hybrid designer alternatives that are readily available and provide a cost-effective solution. If the customer is unable to use one of these devices, we then support the procurement of a different required device.
Are you soldering to the top contact or wire bonding?
This is a must if there are any power discrete devices on the BOM. Many discrete die are available with either option. The rest are only offered with one or the other of these two options. If only solderable top metal is available, and there are no alternative devices, the die distributor can possibly offer a sub-assembly using a Copper or Molybdenum disk with suitable top plating to meet wire bond requirements.
How are you planning to attach the die?
The vast majority of power discretes are available from the manufacturer with solderable back metal only, some with either solderable or gold back metal. If the user is planning to use epoxy attach, it is highly recommended that they not use die with solderable metals. Gold back metal is recommended for either eutectic or epoxy attach. At ES Components we have developed and qualified the ability to remove solderable back metal from wafers and deposit gold for devices where this option is not available from the vendor. Silicon back die are generally epoxy-attached and if a eutectic attach is required, a gold alloy preform is needed.
How will you want this bare die packaged for delivery in full production?
Packaged parts are typically supplied in production quantities on tape-and-reel with nearly infinite shelf life. Waffle packs are the most common medium for shipping bare die, but high volume automatic assemblies are moving towards sawn wafer on film to reduce cost and enhance manufacturing throughput. However, sawn wafer on film has shelf life limitations which demand special management of the supply pipeline. A die distributor can manage the pipeline so that probed unsawn wafers are kept in stock in the appropriate environment and sawn wafers on film are limited to only those wafers needed for short-term production. If there is a delay in manufacturing, the unsawn wafer inventory remains pristine and the shelf life issue is confined to a small subset of the inventory.
Summary
By answering these questions at the time of initial contact and early in the design process, it’s possible to save the user time and money by avoiding the need to modify or redesign the function based on sample evaluation possibly weeks or even months later. We can also properly code the die part number to capture all the pertinent information for future reference.